コベルコ科研・技術ノート
こべるにくす
Vol.32
No.58
- TOP
- 技術ノート「こべるにくす」一覧
- アーカイブス
- 実機を模擬した塗工型全固体電池の試作・評価および解析技術
Technical
Report
B
実機を模擬した塗工型全固体電池の
試作・評価および解析技術
2050 年カーボンニュートラルの達成に向け、日本政府は2035 年までに乗用車の新車販売における電動車の割合を100%にするとの目標を掲げている1)。これに対して自動車メーカーは、リチウムイオン電池を搭載した電気自動車(EV)の販売を進めている。現在使用されている電池は、有機溶剤系電解液をもちいたもの(以降、液系リチウムイオン電池)である。一方でEVの航続距離延長や充電時間短縮の観点からは、より高エネルギー密度、高入出力特性を有する次世代型蓄電池が望まれている。
さまざまな次世代型蓄電池が検討されている中で、近年とくに開発が盛んになっているのが、有機溶剤系電解液を固体電解質に置き換えた全固体電池である2)。全固体電池のカギとなる材料開発においては、イオン伝導率の高さ、活物質/ 固体電解質界面形成の容易さから硫化物系固体電解質が主流となっている。他方、理想的な電池構造を形成する製造プロセスの開発も重要である。従来の液系リチウムイオン電池の製造プロセスをベースに開発が進められているものの、確立した製造プロセスは未だ無い。全固体電池に最適化するとともに、その大型化にも対応した製造プロセスが求められている。
当社ではこれまで次世代型蓄電池の開発促進に向け、固体電解質合成、全固体電池試作から評価解析までのトータルソリューションを構築してきた。現在、実使用を模擬するための大型全固体電池試作設備も整備し、大面積での電極塗工や高圧での接合界面形成など、電池大型化、各層の接合界面形成の最適化に求められるプロセスの開発も可能としている。本稿では、当社が保有する大型全固体電池試作技術を示すとともに、全固体電池の特性最適化に不可欠な電極構造解析技術と内部抵抗解析技術について紹介する。
B-1 実機を模擬した塗工型全固体電池の試作
全固体電池の開発においては、その目的に応じて試作品サイズが使い分けられる。たとえば、硫化物系全固体電池の材料開発、材料選定などの基礎検討においては、作製方法・取り扱いの簡便さから部材を乾式で混合し、プレス・積層により作製する小型の圧粉型全固体電池がもちいられることが多い。一方で、全固体電池の劣化メカニズム解析や安全性評価といった、より実使用に近い条件での評価をおこなうためには、実機を模擬した大型の全固体電池が必要となる。
大型全固体電池の作製プロセスは未だ確立されてはいないが、一つの手法として、液系リチウムイオン電池同様に電極合材をスラリー化し湿式塗工する方法が挙げられる3)。ただ、硫化物系固体電解質は大気中の水分と反応し容易に変質するため、プロセス中の水分混入を抑えなければならない。すなわち、塗工機やロールプレス機といった大型試作設備全般での露点制御がきわめて重要である。
当社が有する塗工型全固体電池試作プロセスおよび環境を第1図に示す。露点-50℃以下に制御したスーパードライルーム内に、露点-80℃以下のAr 雰囲気のグローブボックスを設置し、水分を除去した環境を整えている。この環境により、合材スラリーを混練し集電箔に塗工するプロセスにて大面積の全固体電極シートを作製可能としている。作製された電極シートは低露点環境を維持したまま、ロールプレスによる密度調整や積層・パッキングをおこなえる。活物質/ 固体電解質の接合界面形成においては、等方圧プレス機(Cold Isostatic Pressing; CIP, Warm IsostaticPressing; WIP)を使用し、高圧、加熱下での処理を施すことで、接合界面形成の制御も可能である。
上記設備による試作事例として、塗工型ラミネートセルの外観および同セルの特性評価結果を第2図に示す。ここでは正極活物質にLiNbO3コートLiNi1/3Mn1/3Co1/3O2、負極活物質にグラファイト、固体電解質にLi6PS5Cl、導電助剤にアセチレンブラックをもちいた。0.1C、25℃の充放電において1mAh 程度の放電容量を実現できていることがわかる。これらの技術をベースに数cm 角の塗工型ラミネートセルを作製し、サイクル試験や内部抵抗解析などに供することで、電極構造の最適化や劣化メカニズムの解明などをおこなうことが可能である。
第1図 塗工型全固体電池試作プロセス
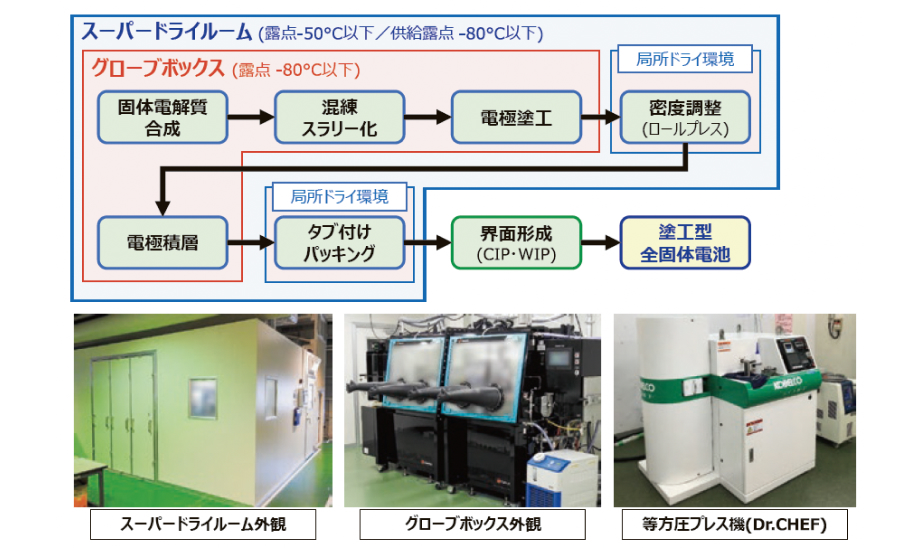
第2図 当社試作の塗工型全固体ラミネートセルの特性
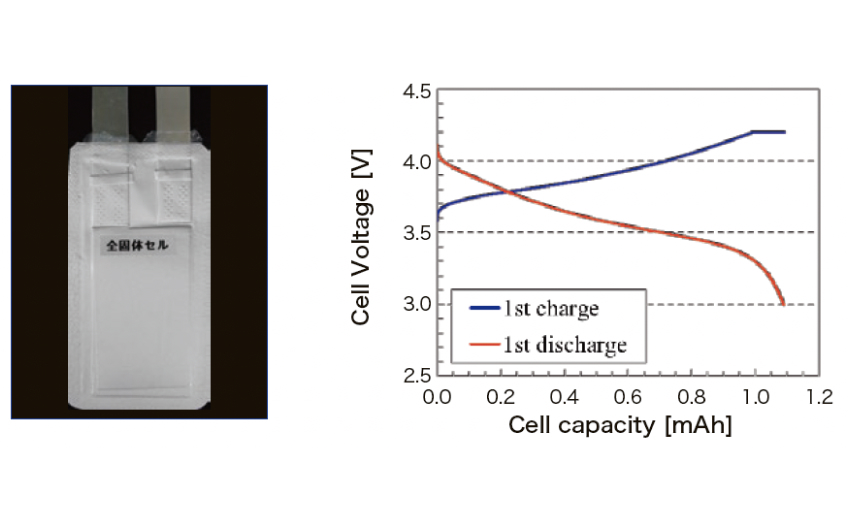
B-2 全固体電池電極の構造評価・解析技術
全固体電池において優れた電池特性をえるためには、材料だけではなく電極の微細構造を詳細に評価し最適化せねばならない。電極内のすべてが固体材料で構成されるがゆえに、材料面ではイオン伝導率の高い固体電解質の合成、活物質/ 固体電解質界面の反応抑制がカギとなる。他方電極構造に関しては、各部材の凝集・偏析の抑制や、空隙や剥離の低減により、電極構造を緻密にすることが重要である4-6)。そのため、構造の評価・解析にもきわめて高度な技術が求められる。
当社では電極構造の評価に対し、試料加工から観察、定量解析まで、全固体電池に特化した一連の取り組みをおこなっている。硫化物固体電解質は熱に敏感なことから、イオンミリングで断面加工する際、イオンビーム照射の影響で容易に変質してしまう。そこで試料の冷却をはじめ加工条件を最適化することで、ダメージのない加工を実現している。全固体電池正極合材層の断面SEM(Scanning Electron Microscope)観察・解析の事例を第3図に示す。ここでは、えられた断面SEM 観察の結果に対してAI 技術を活用した画像解析を施し、構成部材ごとのセグメンテーションをおこなった結果も示している。このように電極の空隙や構成部材それぞれの面積率を算出することで、電極構造を定量的に表現することができる。
正極合材層の分散状態、接触状態の画像解析事例を第4 図に示す。活物質の反応面積や電荷移動抵抗と相関すると考えられる活物質と固体電解質、導電助剤、空隙との接触状態の定量化に関しては、各要素の接触界面を抽出し界面長さを評価することで接触比率として解析した。また、電極反応の均一性と相関すると考えられる電極内の分散状態は、ボロノイ解析により定量化した。これらの手法をもちい電極構造を定量解析し、電極特性やプロセスパラメータとの相関を評価することで、最適な電極構造や作製プロセスの開発に向けた指標がえられる。
第3図 正極合材層の断面SEM観察
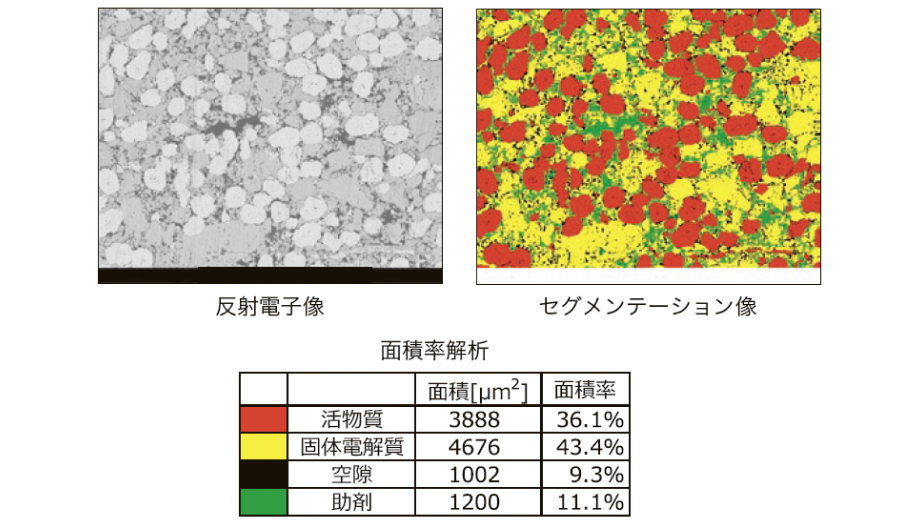
第4図 正極合材層の構造解析
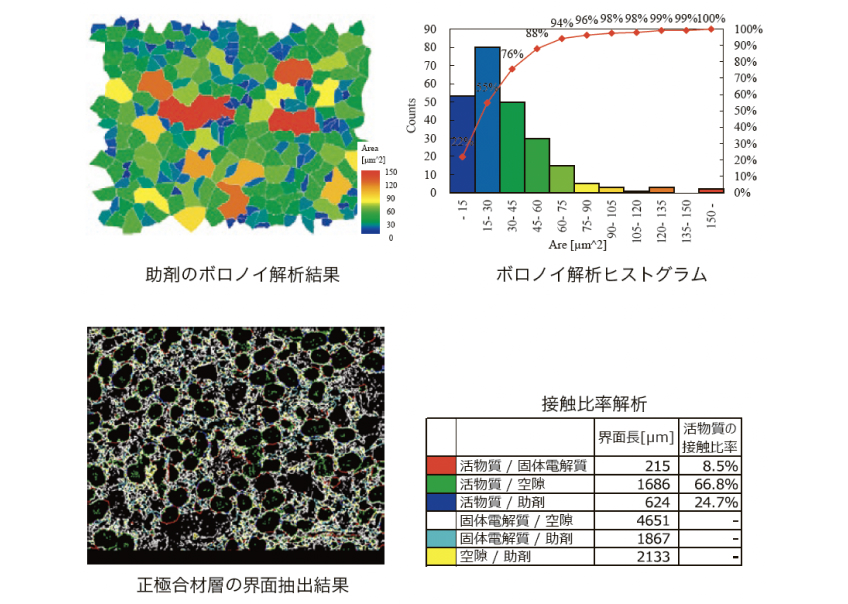
B-3 電極合材中の電子伝導、リチウムイオン伝導の解析技術
全固体電池において高い入出力特性を達成するためには、活物質/ 固体電解質界面での電荷移動反応を如何に促進させるかがカギである。そのためには、活物質/ 固体電解質界面へのリチウムイオンおよび電子のスムーズな供給が必要である。しかしそれらの供給は、第5図の内部抵抗のモデルに示すように電極構造が大きく影響する。そのため液系リチウムイオン電池電極と比較すると、電子伝導パス、リチウムイオン伝導パスの最適化は非常に難しい。これらのことから、内部抵抗を一つひとつの抵抗要素ごとに切り分けたうえで、電極構造との関係を議論することがきわめて重要である。
電子伝導抵抗(Rele) 解析に有効な手法として、走査型拡がり抵抗顕微鏡法(Scanning Spread Resistance Microscopy;SSRM)がある。SSRMはバイアス電圧が印加された試料表面を導電性探針で走査しつつ、探針に流れる電流を計測することで抵抗値の分布を可視化する手法である。これを適用することで電子伝導成分のみを抽出した解析をおこなうことができる。
SSRMの事例として、全固体電池正極合材層の拡がり抵抗マッピング像を第6図に、マッピング像より解析した活物質領域の拡がり抵抗ヒストグラムを第7図に示す。導電助剤が多い電極では、広がり抵抗マッピング像において全体的に低抵抗な領域が広がっている。活物質粒子全体にわたり電子伝導パスが形成されていることがわかる。一方、導電助剤が少ない電極では、低抵抗領域は点在しており、多くの活物質粒子において電子伝導パスの形成が不十分であることがみてとれる。拡がり抵抗ヒストグラムでの比較においても、導電助剤が多い電極ではモードが109 Ω前後にあるのに対し、導電助剤が少ない電極では1012 Ω以上と、定量的にも明確な違いを確認できることがわかる。
第5図 全固体電池電極内の主な抵抗成分のイメージ
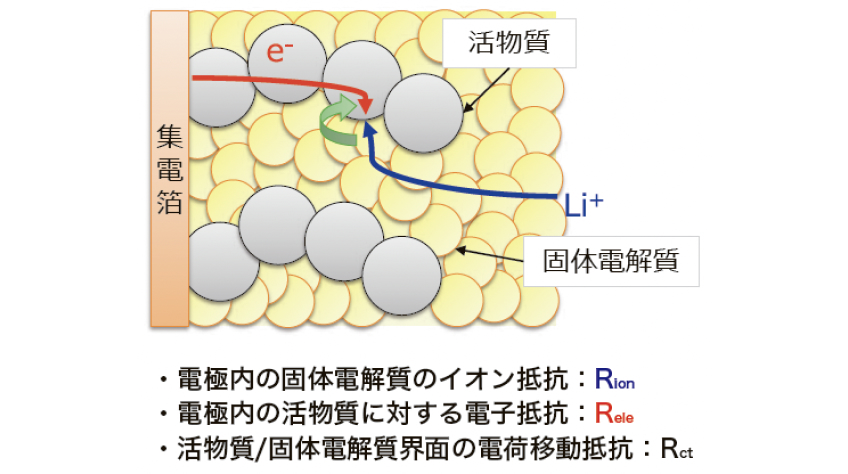
第6図
走査型拡がり抵抗顕微鏡法(SSRM)により
取得した拡がり抵抗マッピング像
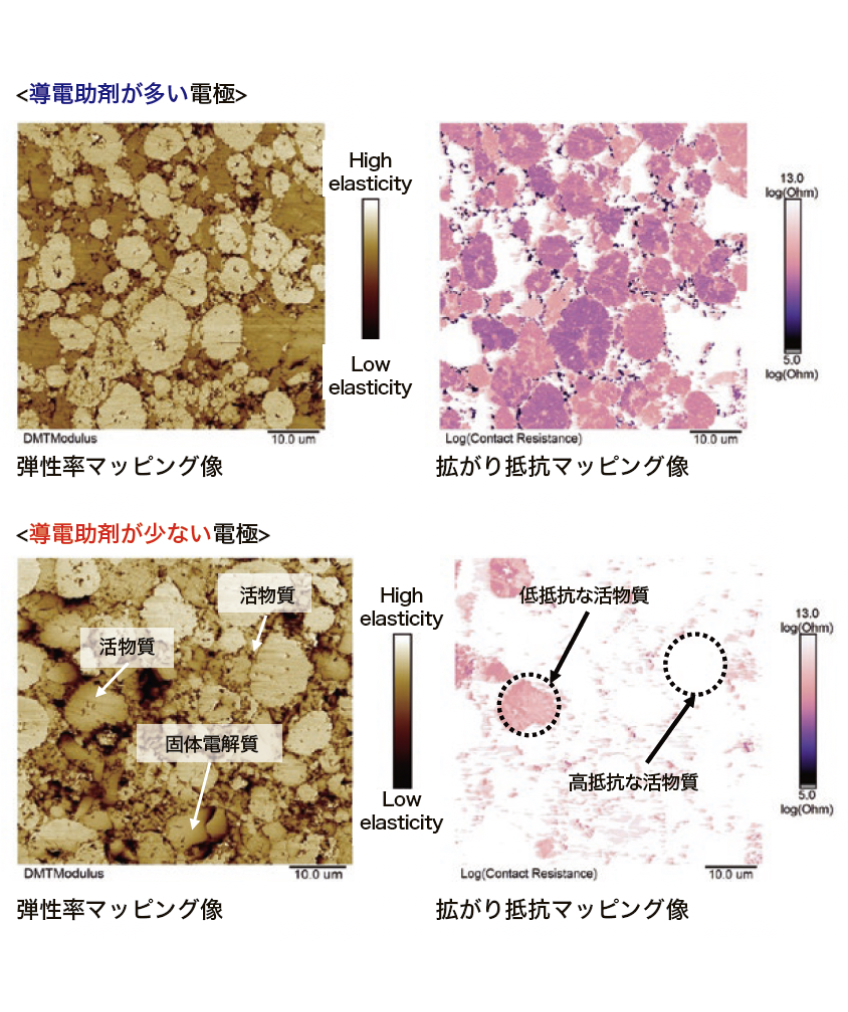
第7図 活物質領域の拡がり抵抗ヒストグラム
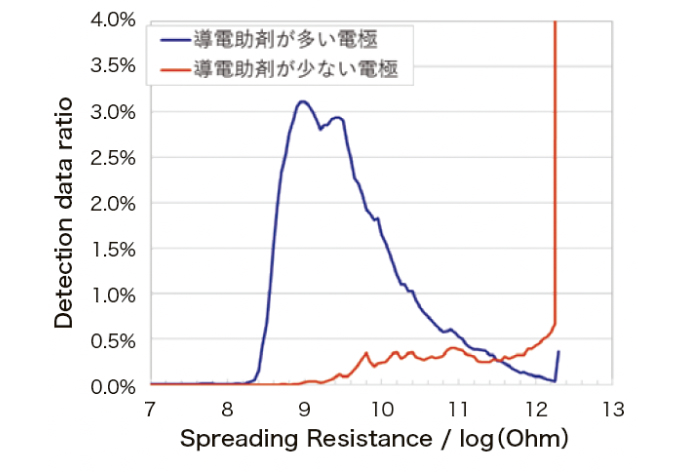
リチウムイオン伝導抵抗(Rion)に関しては、対称セルでの交流インピーダンス測定と伝送線モデルをベースとした解析がおこなわれている7)。この手法は液系リチウムイオン電池においては有効であるが、全固体電池の場合、活物質/ 電解質界面の接触状態が異なることから、同手法をそのまま適用することはできない。そこで当社は、全固体電池の活物質/ 固体電解質界面の状態や電子伝導の影響によるインピーダンススペクトルの形状変化を考慮し、伝送線を変形・拡張させた独自のモデルを考案した(第8図)8-10)。
電極組成の異なる全固体電池正極合材層に対するRion 解析の事例を第9 図に示す。使用した全固体電池電極のRionは固体電解質の体積分率と単純な比例関係とはならず、一方、活物質と導電助剤の体積分率と比較的、相関がみられたことから、電極合材中の電子伝導の状態( 導電助剤の体積割合)の影響を受けている可能性が示唆された。今回の評価の範囲内で最も小さなRionは5Ωで、その電極の導電助剤量は10vol.%であった。
これらの評価結果から推定された正極合材層の電子伝導とRionの関係を第10 図に示す。活物質に対する電子パス形成が良好で導電助剤- 活物質コネクションによる電子供給が支配的な電極では、電極表面近傍の活物質まで電子を供給することができ、電極全体の活物質が反応に寄与することで実効的なRionが小さな値を示していると推定される。一方で、活物質に対する電子パス形成が悪く、活物質- 活物質コネクションによる電子供給が支配的な電極では、電極表面近傍の活物質まで電子を供給することが困難となり、反応に寄与できる活物質が減少することで実効的なRionが大きな値を示したと推定される。
これらの手法をもちい全固体電池電極中の電子伝導、リチウムイオン伝導を解析・定量化し電極特性との相関を評価することで、内部抵抗が低減された最適な電極構造を検討することが可能となる。
第8図 全固体電池のRion解析にもちいた伝送線モデル
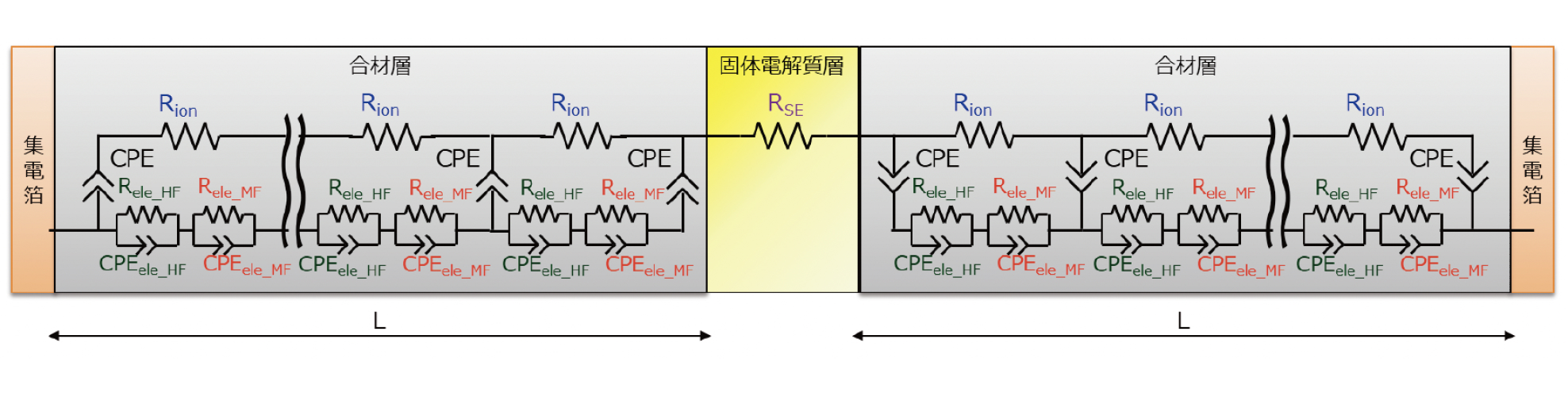
第9図 正極合材層のRion解析結果
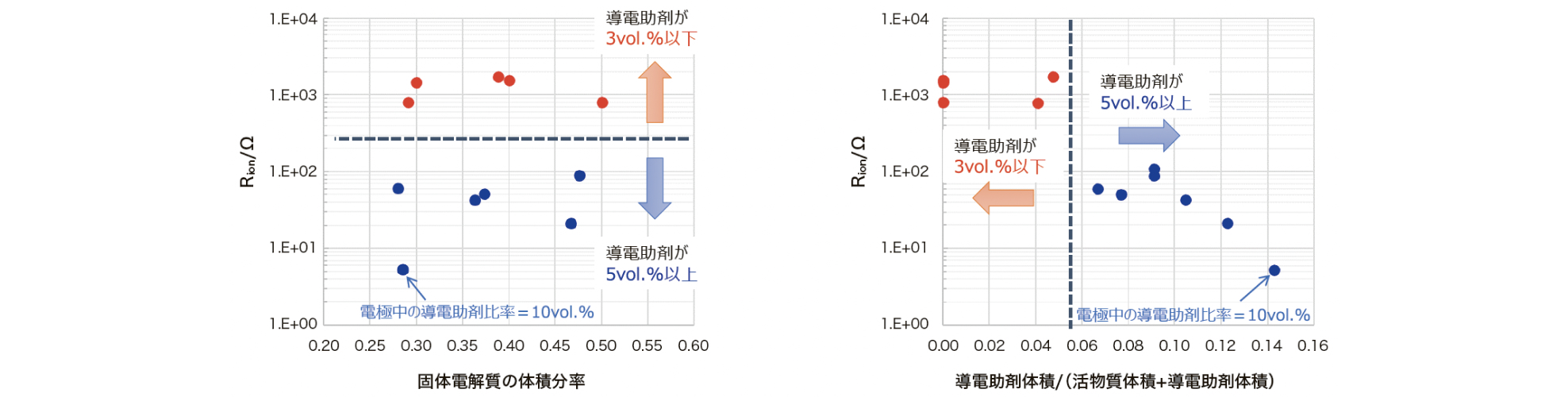
第10図 正極合材層中の電子伝導とリチウムイオン伝導抵抗Rionの関係
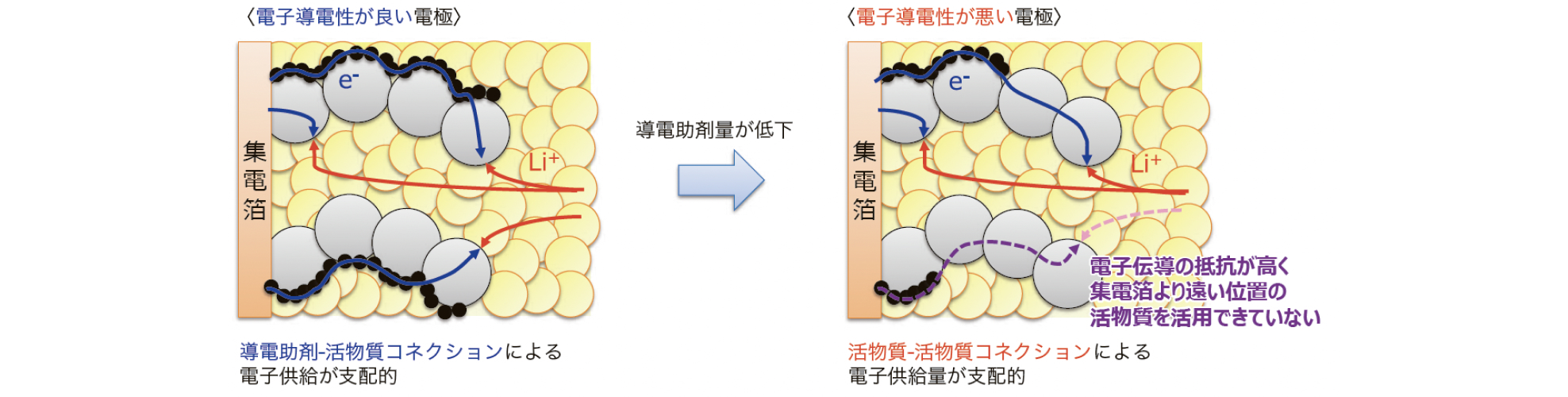
カーボンニュートラル達成に向け全固体電池の実用化を加速させるためには、量産検討と材料評価をつなぐ、実使用・実プロセスを模擬した試作・評価技術が必須と考えられる。本稿では電池特性の最適化に必要な技術として、当社が保有する大型全固体電池の試作および評価解析技術を活用した、大面積電極作製と界面形成技術および電極の構造解析と内部抵抗解析技術について紹介した。
今回紹介した試作技術をベースに、電極を多層化することでさらに高容量な全固体電池を試作し、より実使用に近い寿命評価や安全性評価を可能としていく。またこれらの大型全固体電池の試作・評価技術に加え、これまでに培ってきた全固体電池材料の評価技術も組み合わせることにより、全固体電池の実用化加速に尽くしていく。
参考文献
- *1) NEDO:COP27に向けたカーボンニュートラルに関する海外主要国の動向(2022)
- *2) NEDO:先進・革新蓄電池材料評価技術開発(第2期)2022年度実施方針(2022)
- *3) 日経エレクトロニクス/日経 xTECH 編:次世代電池2019(, 2018), 日経BP
- *4) A. Hayashi et al., Electrochem. Commun., 5, 111 (2003)
- *5) N. Ohta et al., Adv. Mater., 18, 2226 (2006)
- *6) N. Kamaya et al., Nature Mater., 10, 682 (2011)
- *7) K. Kisu et.al, J. Power Sources, 2018, 396, 207
- *8) Z. Siroma et.al, J. Power Sources, 2016, 316, 215
- *9) 阿知波敬ほか:第61回電池討論会,2F06 (2020)
- *10) 阿知波敬ほか:第64回電池討論会,2F06 (2023)