コベルコ科研・技術ノート
こべるにくす
Vol.32
No.58
- TOP
- 技術ノート「こべるにくす」一覧
- アーカイブス
- EV車両のバッテリーパックを対象とした衝突安全・電池安全性連成シミュレーション
Technical
Report
I
EV車両のバッテリーパックを対象とした
衝突安全・電池安全性連成シミュレーション
EV 車両の衝突事故において、車両の変形だけでなく車載用バッテリーにも変形がおよんだ場合、バッテリー内での短絡の発生により急速な発熱・発火が 生じる危険性がある。このような現象をシミュレーションで予測する技術は、EV 車両の構造設計において有用であると考えられる。
本稿では、EV 車両のベンチマーク調査の際に取得した海外製EV 車両の3Dスキャンデータをもとに、CAE(Computer Aided Engineering) モデル化した車載バッテリーパックの衝突安全・電池安全性連成シミュレーションを実施した。本結果より、衝撃圧壊と電池熱暴走条件との関係を考察した事例を紹介する。
I-1 バッテリーパックのモデル化
衝突安全性評価の対象となるバッテリーパックの数値解析用モデルを構築するには対象物の3次元形状データ(CADデータ)が必要となる。ここでは海外製EV 車両のバッテリーパックを対象として実機を解体しながら3次元形状測定を行い、形状データを基にサーフェス化を行ってCADデータを作成した。3次元形状測定にはハンディタイプの非接触式3Dスキャナー(精度: 最大0.050 mm)を使用した。第1図に対象とした実機バッテリーパック、そのスキャン形状およびサーフェス化したCADデータを示す。なお、CADデータ化の範囲は、衝突安全性能に寄与する構造部材のみを対象とした。このCADデータをもちいて、第2図に示すCAE 用のメッシュモデルを作成し、衝突安全性の評価を目的とした数値解析を実施した。モデル規模は、節点数:約130 万、要素数:約 150 万である。
第1図 実機バッテリーパックからのCADデータ作成
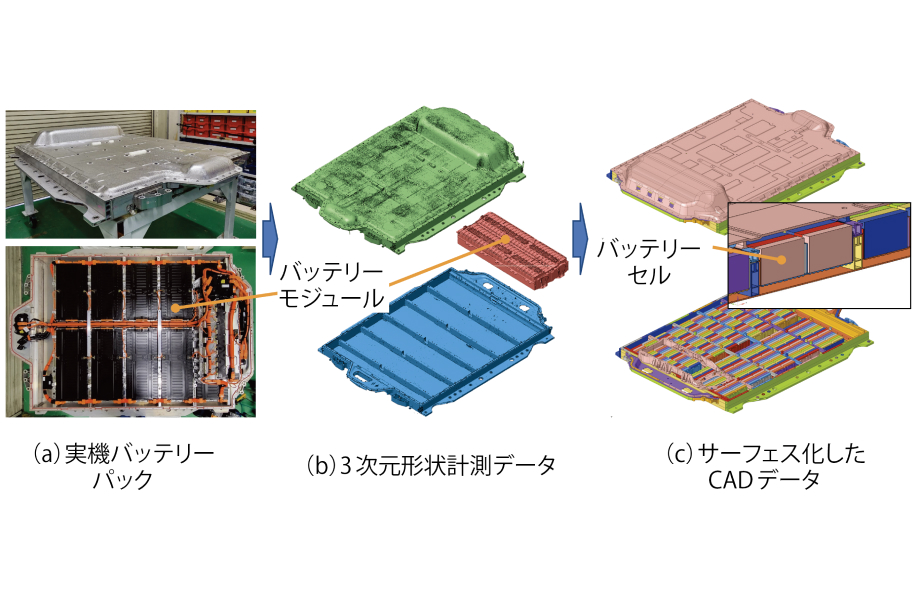
第2図 CAE用メッシュモデル
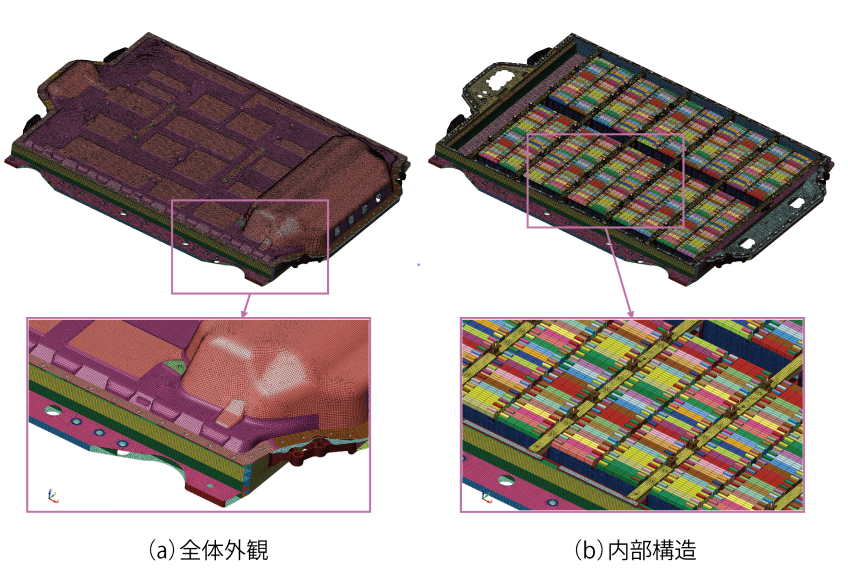
I-2 CAEによる衝突安全性評価
自動車の衝突安全性評価の基準は国や地域によって異なる。一般的には、フロント、サイドおよびリアなどの代表的な3方向に対する衝突試験があり、自動車事故の際に乗員や歩行者などの被害を最小限に抑えるための性能が要求される。しかしながら、EV 車においては、車両に搭載されたリチウムイオンバッテリーの熱暴走による火災のリスクもあり、バッテリーパック自体の衝突安全性も考慮することが望まれる。そこで、バッテリーパックのみに着目した衝突変形性能を数値解析により確認した。ここでは代表的な3方向のうち、バッテリーパックに波及する衝突変形が最も懸念されるサイド試験について確認した。第3図にバッテリーパック側面へのポール衝突を模擬した衝突条件を示す。
本来は車体全体に対する衝突安全性評価であるが、バッテリーパックの耐衝突性能に関する設計思想を理解するため、バッテリーパック単体の衝突現象を解析することとした。ここでは、バッテリーパックの質量によって生じる運動エネルギーを吸収して安全 性が保てるか否かを確認した。
衝突速度はポール側面衝突試験(UN-R135)を参考にした32 km/hと、過大な条件として約2倍の60 km/hとした。CAEは汎用有限要素解析ソルバーのAnsys LS-DYNA(以下、LS-DYNA)を使用した。
第4図に衝突速度32 km/hにおけるバッテリーパックの変形状況を示す。ポールとの衝突部においてバッテリーパックの側面フレームがパック内部に湾曲していることが確認できる。なお、この変形は側面フレームとバッテリーモジュール間に設けられた空間内で留まっており、バッテリーモジュールには影響しないと判断される。このことから、この空間はクラッシャブルゾーンとして意図的に設けられた、側突によるフレームの変形がバッテリーセルに到達しないようにすることで安全性を確保した設計と推測される。
第3図 衝突条件
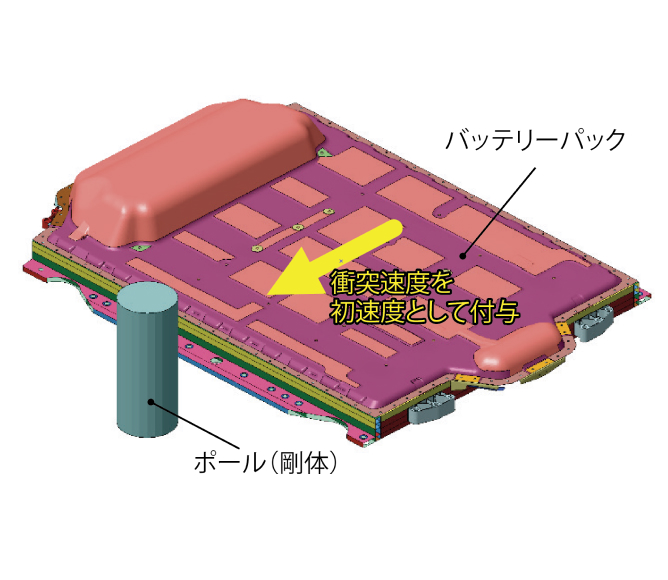
第4図 衝突速度32 km/hにおける変形状況
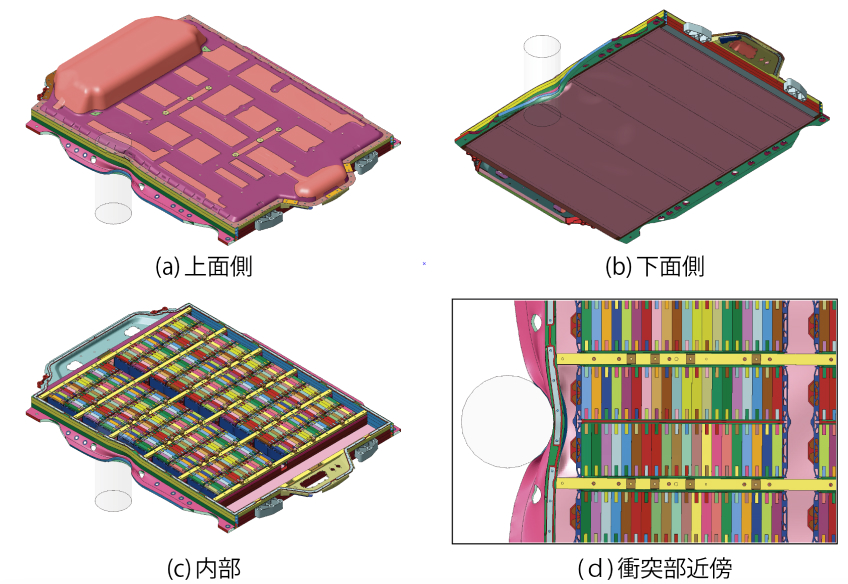
次に、UN-R135よりも過大な条件で衝突した場合の確認を行った。第5図に衝突速度60 km/hにおけるバッテリーパックの変形状況を示す。60 km/h 衝突では、側面フレームの変形がバッテリーモジュールに到達し、端部のセルに圧縮変形が生じていることが確認できる。よってクラッシャブルゾーン内では変形を吸収しきれていない。衝突速度60 km/hは運動エネルギーが32 km/h 衝突の約4倍となり、この圧縮変形によりバッテリーセルが短絡して熱暴走を引き起こす懸念がある。本バッテリーパックの構造としては、車体左右方向に分散配置されている各モジュール間 (パック中央)にも側面と同様な空間が設けてある。よって、側面からモジュールに到達した変形もモジュール自身の剛体運動(スライド運動、第5図(d))で吸収され、セルが受ける荷重が少なくなるよう工夫された構造と推測される。
以上のように、ベンチマーク調査とCAEは、自社製品の優位性や競合他社との差別化要素を見つけ出す有効なツールである。すなわち、さまざまな条件下での応答や挙動を評価することで、その設計思想の解明に役立つと考える。
第5図 衝突速度60km/hにおける変形状況
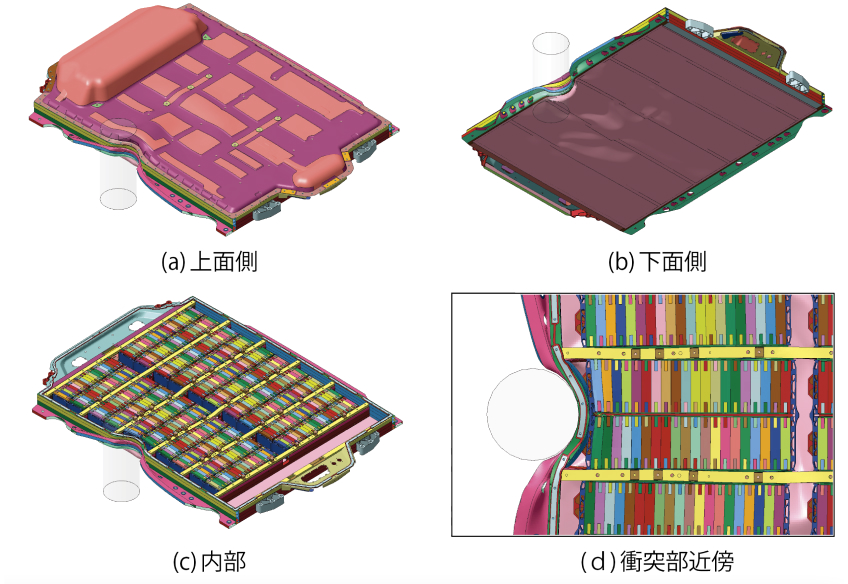
I-3 CAEによる短絡熱暴走評価
LS-DYNAの構造・熱・電磁場(Electoromagnetic、EM) 連成解析ソルバーを使用し短絡熱暴走のシミュレーションを行った。従来のシミュレーションでは積層構造のセルに対して各層の詳細なモデル化が必要であるが、LS-DYNAにはBattery macro モデル(Batmacモデル1))が実装されている。Batmacモデルは各節点にRandles 型等価回路(第6図(a))を考慮することで各層の詳細なモデル化が不要であり、効率良く短絡や熱暴走を表現可能なため、ここではBatmacモデルを使用することとした。
短絡や熱暴走はセル内の反応によって生じる複雑な現象である。熱・EM 解析で要求される時間刻みは、一般的な短時間の衝突解析に比べて長い現象のため、一連の連成解析には多大なコストを要する。そこで、今回のシミュレーションでは、衝突解析の変形状態を熱・EM 解析の初期形状としてマッピングし、短絡はマッピング後のひずみ分布、熱暴走は短絡後の温度変化をもとにモデル化することで、実用的な時間でのシミュレーションを可能とした。
3.1 単セルを対象とした解析
最初に、単セルを対象にBatmacモデルをもちいた短絡熱暴走シミュレーションを行った。シミュレーションにもちいる機械的特性は衝突解析と同じとし、伝熱特性および電気特性は各部材の材料に応じた一般的な物性値を使用した。セルの容量(=57 Ah)、電圧とSOC(State of charge)の関係(第6図(b))は測定値を使用した。Randles 型等価回路のパラメータはR0=R10=0.001、C10=1000とした。短絡は衝突解析によりえられたひずみ分布をもとに、セルのひずみが10 %を超えた領域で発生する条件とした。熱暴走は短絡後の温度が200℃を超えた領域で発生するとした。
第6図 Randles型等価回路、電圧とSOCの関係
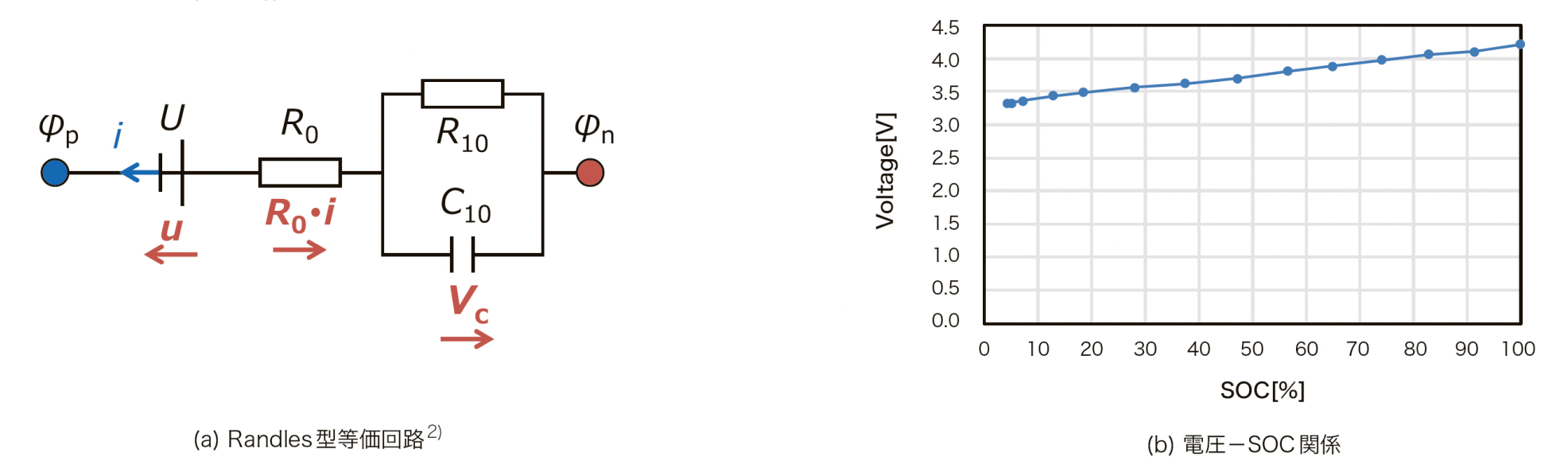
第7図に(a)初期ひずみ分布、(b)SOC 分布、(c)ジュール熱分布を示す。(a)図と(b)図、(c)図を見比べると、ひずみが大きい領域で短絡が生じてSOCが減少し、セル内に大きな電流が流れたことでジュール熱が大きくなっていることがわかる。
第8図にセル上部タブ間の温度履歴を示す。変形直後40 秒手前までは短絡による温度上昇が生じ、200℃を超えたあたりの急激な温度上昇は熱暴走によるものである。その後、所定の熱量に達したところで温度上昇がとまり熱暴走が終了している。このように、Batmacモデルをもちいると、短絡熱暴走の現象がシミュレートできることが確認された。
第7図 初期ひずみ分布、SOC分布、ジュール熱分布
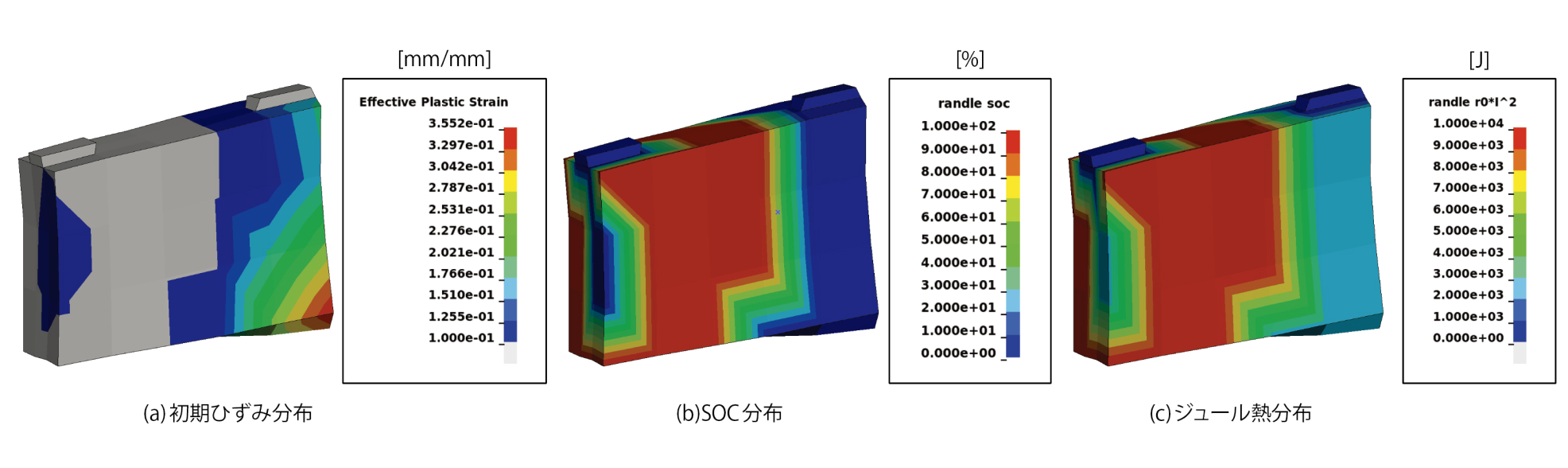
第8図 セル上部タブ間の温度履歴
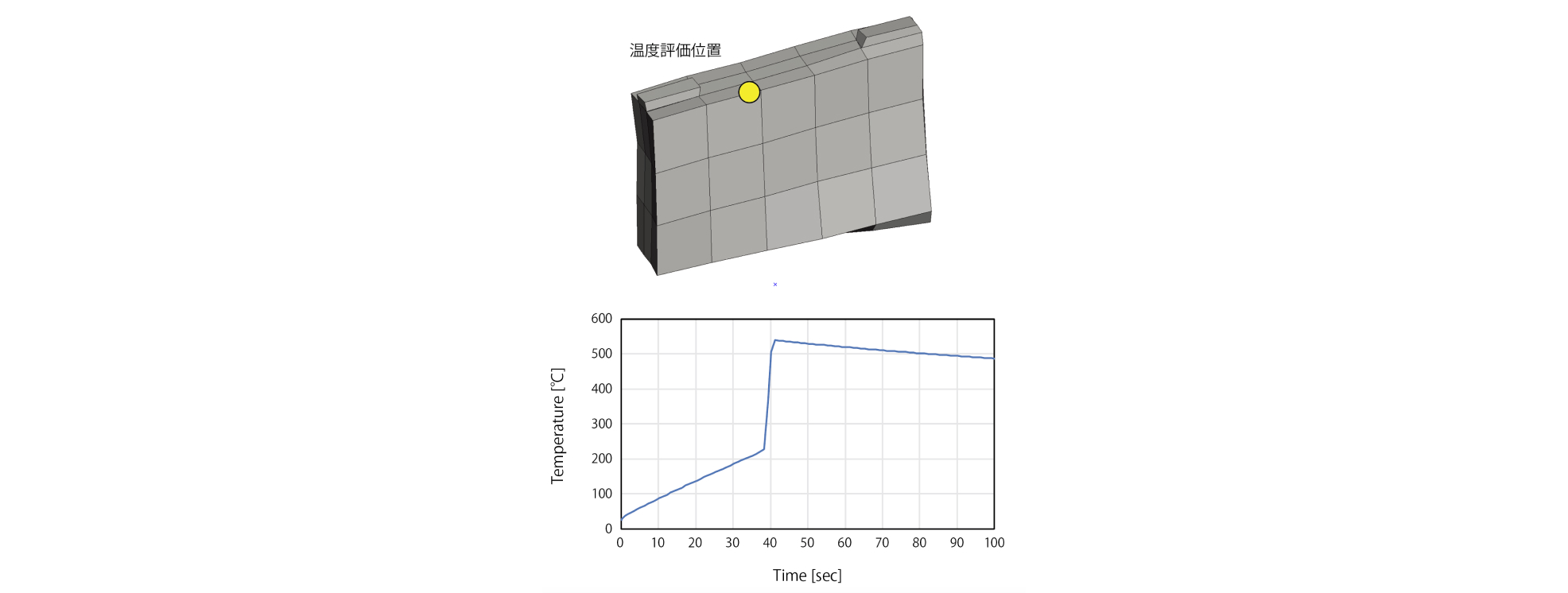
3.2 バッテリーパックを対象とした解析
次に、2 章の衝突速度60 km/hの解析結果をもとに、バッテリーパックを対象として3.1 節で設定したパラメータをもちいて短絡熱暴走シミュレーションを行った。セル間や各部材間には接触熱伝達を考慮し、バッテリーパックの周囲には空気との熱伝達を考慮した。
第9図に(a)初期ひずみ分布、(b)SOC 分布、(c)電流分布を示す。(a)図に示すように衝突によるひずみは衝突部から2番目のセルにもおよんでおり、(b)図、(c)図と比較すると、単セルでの解析と同様、短絡領域でSOCの減少と大きな電流が流れていることがわかる。
第9図 初期ひずみ分布、SOC分布、電流分布
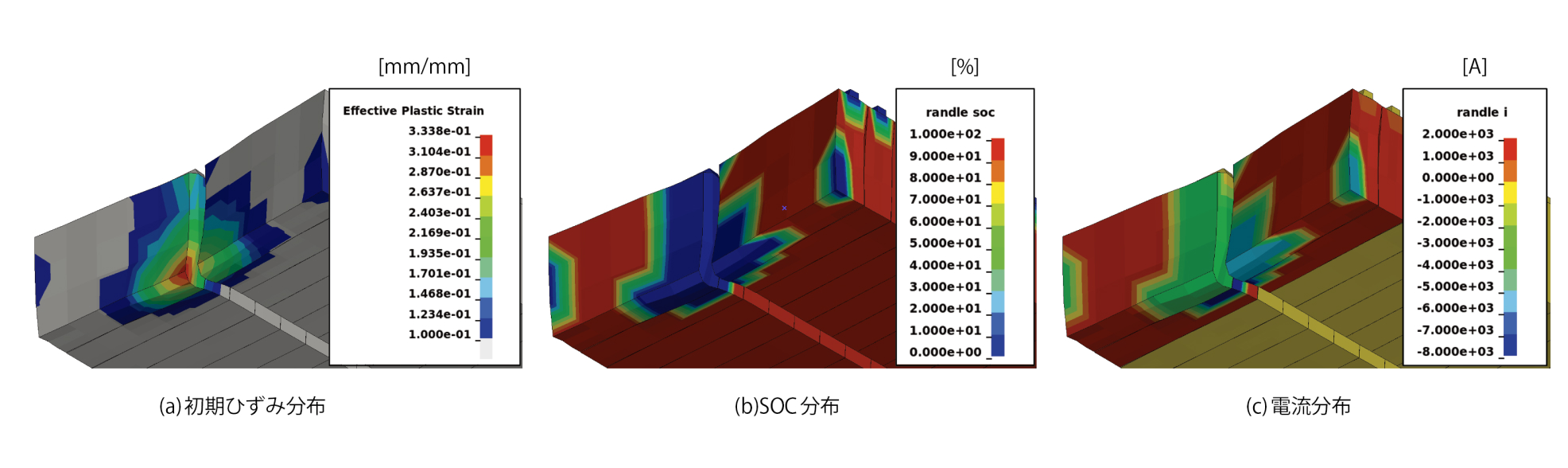
第10 図に代表セルの上部タブ間の温度履歴を示す。衝突部から1番目のセル①は短絡開始直後から温度が上昇し、200℃を超えたあたりで熱暴走が生じている。5番目のセル⑤では温度上昇が始まって間もなく急激に温度が上昇している。このように衝突部のセルで短絡熱暴走が起きた場合、熱伝導によって衝突部から離れたセルへ熱暴走が連鎖し、480 秒後には1モジュール分熱暴走が生じた。
第10図 代表セル上部タブ間の温度履歴
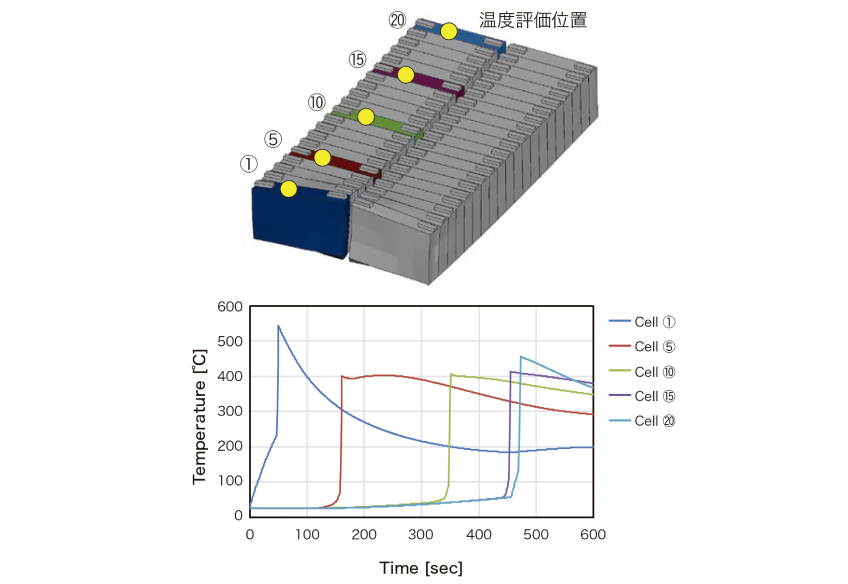
第11 図に短絡開始からの所定の経過時間に対する温度コンターを示す。時間の経過とともに衝突部から離れたセルの温度が上昇していく様子がわかる。なお、温度が高くなったのは1モジュール分であることから、今回対象としたバッテリーパックはモジュール間で温度拡散が生じ難い構造になっていると推測される。
以上のように、Batmacモデルを使用することで、バッテリーパック全体を対象とした短絡熱暴走現象が実用的な解析コストで可能となった。
第11図 代表時刻の温度コンター図
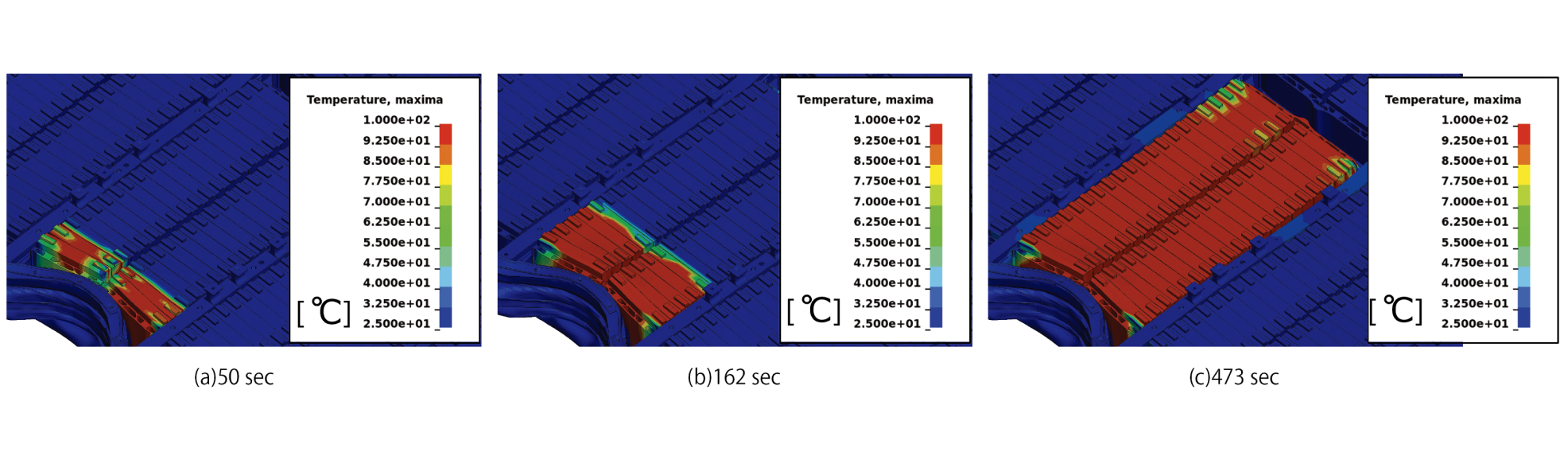
本稿では、EV 車両の3Dスキャンデータから数値解析モデルを作成し、車載バッテリーパックの衝突安全・電池安全性連成シミュレーションを行った。本技術により、バッテリーパックの構造安全性や材料選択など、製造工程のデジタル化が進み、設計コストや試作工数の削減に寄与することが期待される。
参考文献
- *1) LS-DYNA KEYWORD USER'S MANUAL VOLUME III、 Multi-Physics Solvers、LS-DYNA R13、LST、AN ANSYS COMPANY.
- *2) P.L'Eplattenier, et al. : 12th European LS-DYNA Conference( 2019).