コベルコ科研・技術ノート
こべるにくす
Vol.33
No.60
- TOP
- 技術ノート「こべるにくす」一覧
- アーカイブス
- ホットスタンプ材の圧壊試験と衝突CAE
Technical
Report
E
ホットスタンプ材の圧壊試験と衝突CAE
近年の自動車ボディでは電動化対応のため軽量化が図られており、ホットスタンプ材は強度を活かして骨格系部材への利用が進んでいる。ホットスタンプ材は熱間でプレス成型し,成形金型に挟んだ状態で急冷させることにより強度を確保する。いっぽうで高強度化のために炭素量を増加すると割れやすくなることが知られている1)。
そこでホットスタンプ材の破断特性を引張試験で取得し、その違いを確認した。また軸圧壊試験を行い、割れ挙動についてデジタル画像相関法( Digital Image Correlation:DIC )をもちいて詳細に観察した。また有限要素法( Finite Element Method:FEM )をもちいた数値解析により破壊を考慮した軸圧壊シミュレーションを実施し、割れ挙動の比較を行った。
その結果、精度よく割れ挙動を再現できたので本稿にて紹介する。
E-1 ホットスタンプ材の作製
ホットスタンプ材を真空誘導炉で溶製し、板厚1.2mmの冷延鋼板を作製した。炭素量は0.2,0.3,0.4wt.%の3種類とし、それ以外の成分は同じとした。作製した冷延鋼板について、ホットスタンプ工法での焼入れを模擬して930℃にて300秒の加熱後にダイクエンチによる冷却を実施した2)。試作板の機械的特性を第1表に示す。引張強度は、0.2%Cが1349MPa、0.3%Cが1698MPa、0.4%Cが2087MPaであった。伸びは3材種とも7%弱であり、C量の違いによる顕著な影響は認められなかった。第1図に焼入れ後の走査型電子顕微鏡による母材組織写真と後方散乱電子回折( Electron Backscatter Diffraction、以降EBSD )によるPhase mapを示す。母材組織はマルテンサイト組織を有しており、C量の増加にともない炭化物の析出が促進されていることが確認される。また、Phase mapでは緑色をα相、赤色をγ相で表示しており、相分率の結果よりγ相が0.1%と少ないことからマルテンサイト単相の組織と判断された。
第1表 ホットスタンプ材の機械的特性
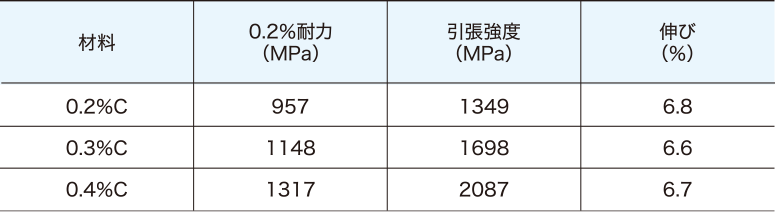
第1図 組織写真およびPhase map
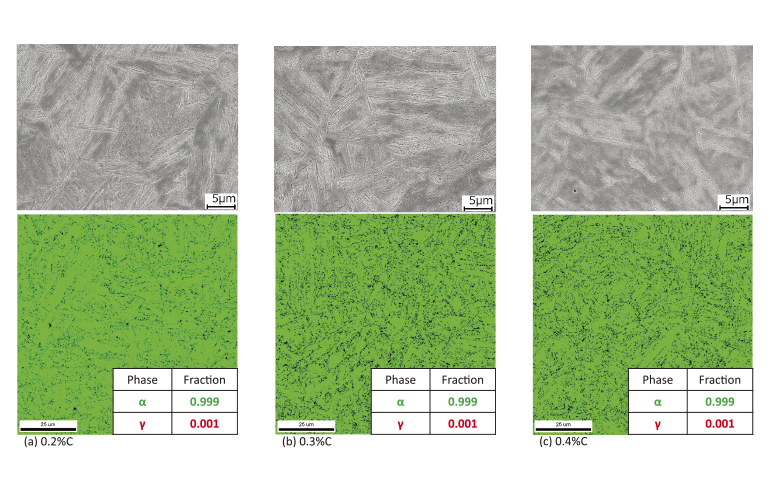
E-2 破断特性取得のための材料試験
自動車の衝突解析では応力三軸度ηに代表される応力状態に依存した破断モデルがもちいられることが多い。そのための試験方法がいくつか報告されており、本件ではせん断試験、単軸引張試験、切欠き付き試験片の引張試験、および張出試験の4種類の試験をおこなった。これらの試験で応力三軸度は、それぞれ、せん断( η= 0 )、単軸引張( η= 1/3 )、平面ひずみ ( η= 1/√3 )、および等二軸( η= 2/3 )に相当する。引張試験は島津製作所社製万能試験機を使用し、張出試験は東京衡機試験機社製深絞り試験機を使用した。ひずみ計測にはGOM社製DIC装置ARAMISを使用し、試験片表面にランダムパターンを塗布して試験片破断時までひずみを測定した。
各試験で得られた荷重-変位線図を第2図に示す。なお、図横軸の変位は、破断位置を基準に設定した2点間距離の変化とした。張出試験の変位は、成形頂点の変位量とした。第2図(a)のせん断試験の結果、0.2%Cは試験終盤に荷重が低下して破断したが、0.3%C、0.4%Cでは荷重低下は認められなかった。第2図(b)の単軸引張試験の結果、3材種とも最大荷重到達後の荷重低下( 局部変形 )が見られ、C量が増加するにともない破断時の変位量( ピーク荷重到達時からの変位量 )は減少した。第2図(c)の切欠き付き引張試験の結果、0.3%Cおよび0.4%Cの破断時の変位量は0.2%Cの破断時の変位量に比べ極端に小さく、2材種間で同程度であった。第2図(d)の張出試験の結果から、炭素量の増加にともない変位約10mm以降の荷重-変位関係の勾配が大きくなった。以上、4種類の試験を通じて、炭素量が増えるに従い破断した変位量が小さくなることが確認された。
第3図は、切欠き付き試験片の引張破断直前の最大主ひずみ分布画像である。破断時の変位量が大きい0.2%Cでは切欠き底部付近にひずみが集中しているのに対し、0.3%C、0.4%Cでは0.2%Cほどの高ひずみ分布は生じなかった。これは、第1図に示した破断時の変位量の大小関係と整合している。また、ひずみは切欠き部の最小断面に必ずしも集中しておらず、載荷直交方向から若干傾いている様相であった。このように、DICを用いることによって、炭素量による破断直前のひずみ量やひずみの集中状況の違いを視覚的に確認できた。
第4図は、単軸引張、切欠き付き引張、および張出試験における破断直前のひずみを比較したものである。なお、単軸引張、切欠き付き引張試験では2点間変位から算出したひずみを、張出試験では破断部のひずみをポイントで抽出した。これより、3種類の試験で破断ひずみの炭素量による変化を確認でき、切欠き付き引張で0.2%Cと0.3%Cで明確な差が見られた。また、張出試験では0.2%C、0.3%Cの破断ひずみは同程度であるのに対し、0.4%Cは他の2材種より破断ひずみが著しく小さかった。0.4%Cでは、3種類の試験によらず、破断直前のひずみは0.14前後であった。
このことから、ホットスタンプ材において炭素量による破断挙動への影響は応力三軸度η=1/3より大きい領域で顕著になることが分かった。
第2図 各種破断試験の荷重-変位線図
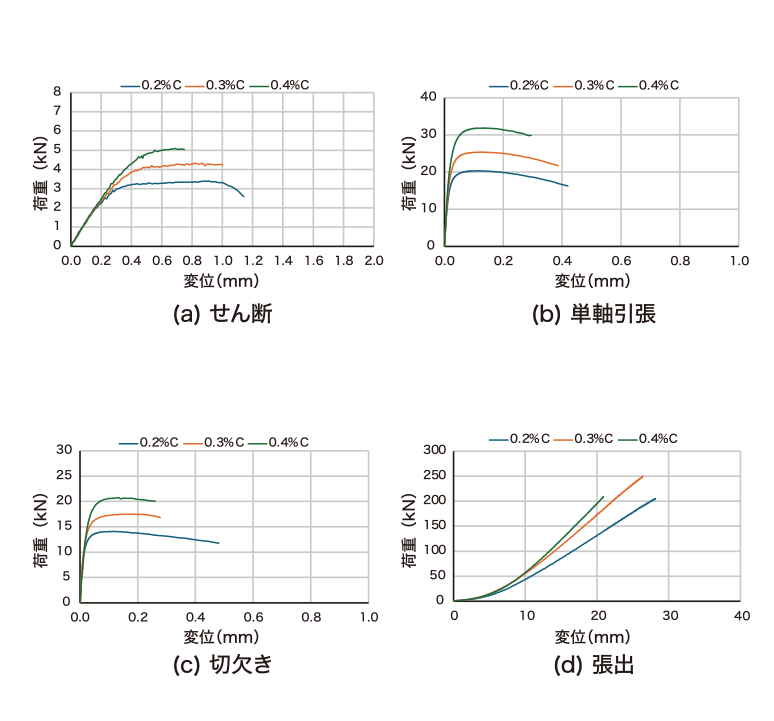
第3図 破断直前の最大主ひずみ分布画像(代表:切欠き)
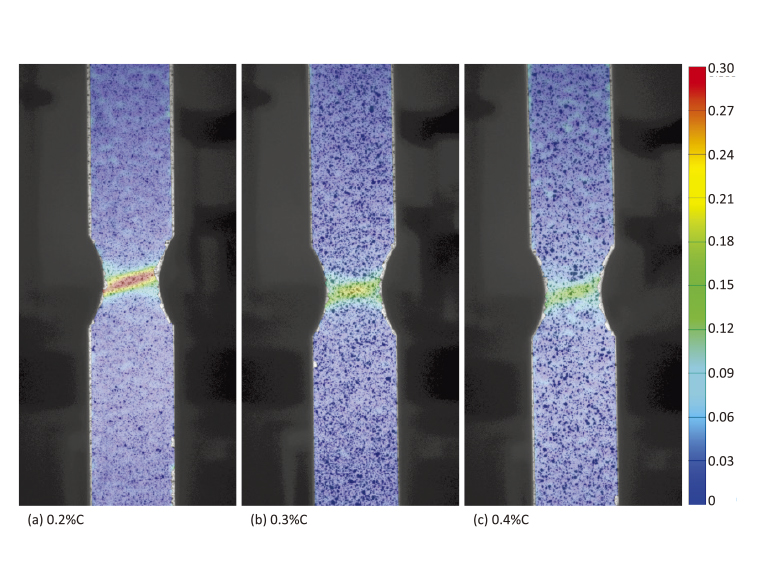
第4図 炭素量と破断ひずみの相関
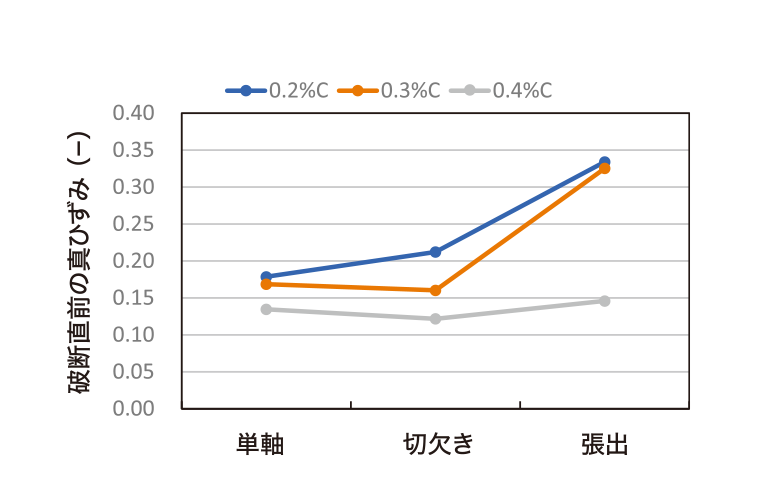
E-3 軸圧壊試験とDICによるひずみ計測
作製したホットスタンプ材をもちいて軸圧壊試験用ハット型試験体を作製した。試験体は断面50×50mm、長さ200mm、曲げR5mmとして、共材の上下板をスポット溶接で接合した。また試験体端部に天板地板を溶接接合した。試験機はアミノ社製の1000tonプレス機を使用した。軸圧壊試験は試験速度を1mm/secとした準静的な負荷を与え、荷重とストロークを取得した。
また、ARAMISをもちいてひずみ計測を実施した。試験体にランダムパターンを塗布し、ハット凸部の変形部のひずみを計測した。
第5図に軸圧壊試験後(ストローク90mm位置)の試験体の変形および破断状況を示す。0.2%Cと0.3%Cでは蛇腹状変形部で破断せず変形が進行しているが、0.3%Cは典型的な蛇腹状変形とはやや様相が異なっている。0.4%Cについては大きな破断を伴う変形となった。
第6図に各炭素量での軸圧壊試験中の変形状況を示す。ストローク1.6mm位置では、すべての試験体で同様な座屈変形が認められる。また、0.4%Cでは変形部近傍のスポット溶接部に破断が認められた。ストローク約11mm位置では、0.4%Cにおいてハット肩近傍にき裂が生じ、ストローク約20mm位置では同き裂の進展が認められた。ストローク90mm位置では、このき裂の進展の影響を受け大きな破断を伴う変形が生じたと推察される。とくに0.4%Cは、引張破断試験の結果においても破断直前のひずみ量が他の2材種より低かったことから、早期にき裂が生じたことが示唆される。0.2%C、0.3%Cではストローク約11mmで、破断が認められず、2材種とも同様の変形状態であった。ストローク約20mmで、0.2%Cでは座屈変形部中央が凹状に変形しており、中央基準に座屈が進展することによりストローク90mmで典型的な蛇腹状変形が生じたと考えられる。また、0.3%Cでは座屈変形部下側が凹部に変形しており、凹部基準に変形したためストローク90mmでは上板が覆いかぶさるように変形したと考えられる。
第5図
軸圧壊試験後の試験体の変形および破断状況
(ストローク90mm位置)
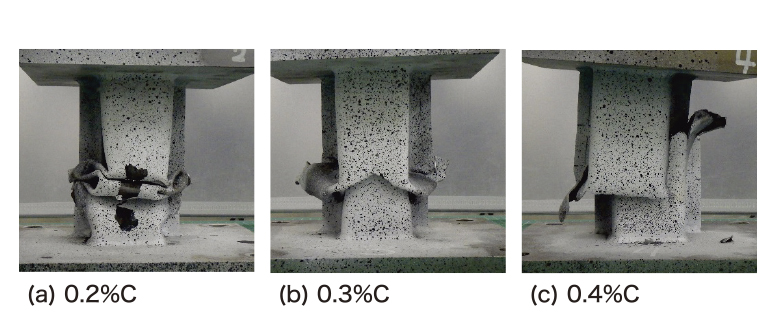
第6図 軸圧壊試験中の試験体の変形状況
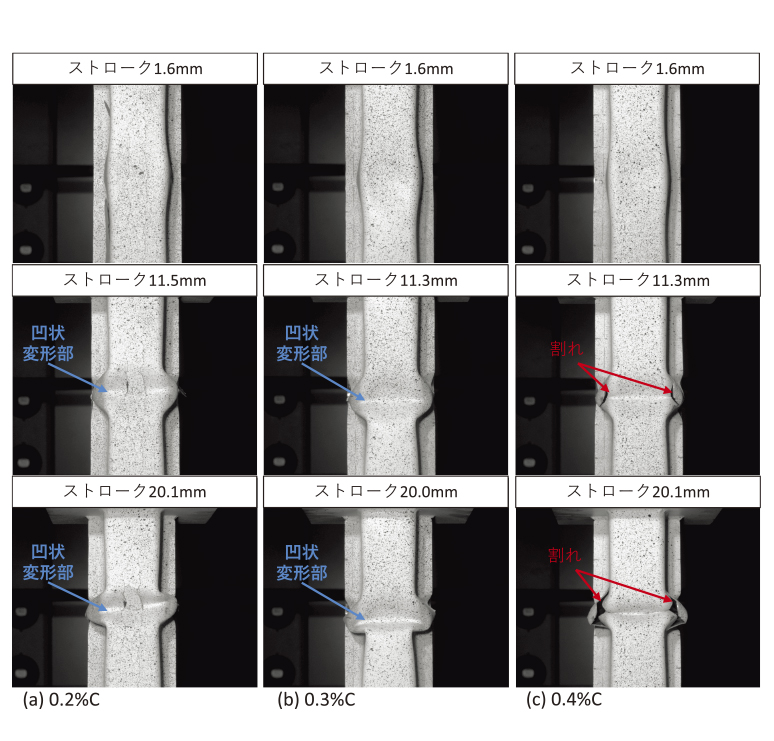
E-4 軸圧壊解析
軸圧壊解析のFEMモデルはハット部にはシェル要素をもちい、メッシュ寸法は1mm,弾塑性体でモデル化した。また天板地板はソリッド要素をもちいた弾性体、試験機の治具は剛体要素でモデル化した。使用したソフトはSIMULIA Abaqus/Explicitであり、動的陽解法で計算を実施した。ホットスタンプ材の材料モデルは、ミーゼスの降伏関数による等方弾塑性体を仮定した。破断モデルは、応力三軸度を基準としたY.Baiらのモデル3)を採用した。破断モデルのパラメータは前項の4種類(せん断、単軸引張、切欠き付き引張、張出)の破断特性試験をもとに調整のうえ決定した。
軸圧壊解析の結果得られた荷重-ストローク関係とエネルギー吸収量の推移を第7図に示す。これらの結果から、試験での各挙動の推移を概ね再現できおり、解析の再現性が高いことがわかる。次に、ストローク1.5~20mmと90mmのときの変形状態を第8図、第9図に示す。カラーは相当塑性ひずみ分布を示している。ストローク1.5mmではいずれも軸方向中央部付近で座屈している。ストローク12mmでは0.4%Cにおいては座屈変形した肩部付近で割れが発生しており、割れ挙動は試験とよく一致した。ストローク90mmでは0.2%Cでは蛇腹変形し,0.3%Cでは蛇腹変形の途中でハット部が部分的に破壊、0.4%Cでは座屈部付近から大きく破壊した状態となって、試験の変形挙動をよく再現することができた。
最後に、0.4%Cを例として、ストローク20mmまでの発生ひずみを、DICとFEMで比較した。第10図は、凹み部、幅方向17mmの肩部および上側17mmにおける軸方向ひずみの発生状況である。結果、凹み部と肩部はストロークおおよそ9mm以下の範囲、上側についてはストローク15mm程度までよく一致しており、座屈の初期過程の挙動がFEMで再現できた。ただし、たとえば凹み部のストローク9mm以降のように、FEMで破断が生じた場合にはそれ以降のひずみの直接比較は困難となる。
第7図 軸圧壊解析 荷重−ストローク線図と吸収エネルギー線図の比較
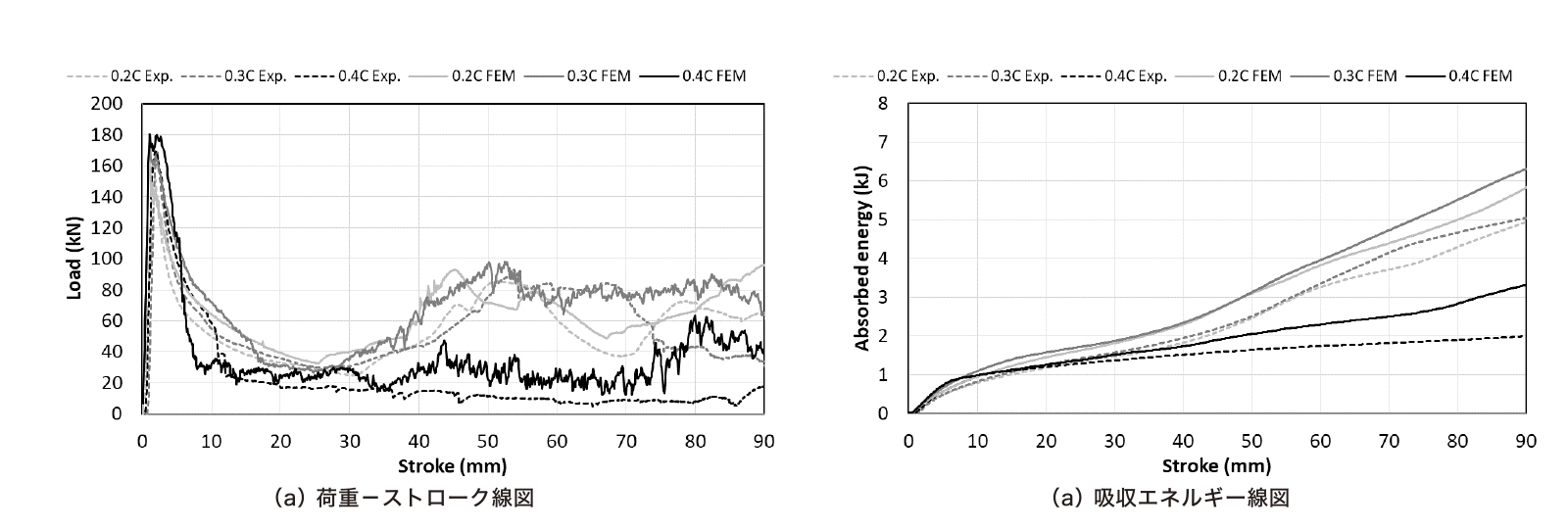
第8図 各ストロークでの相当塑性ひずみ分布図
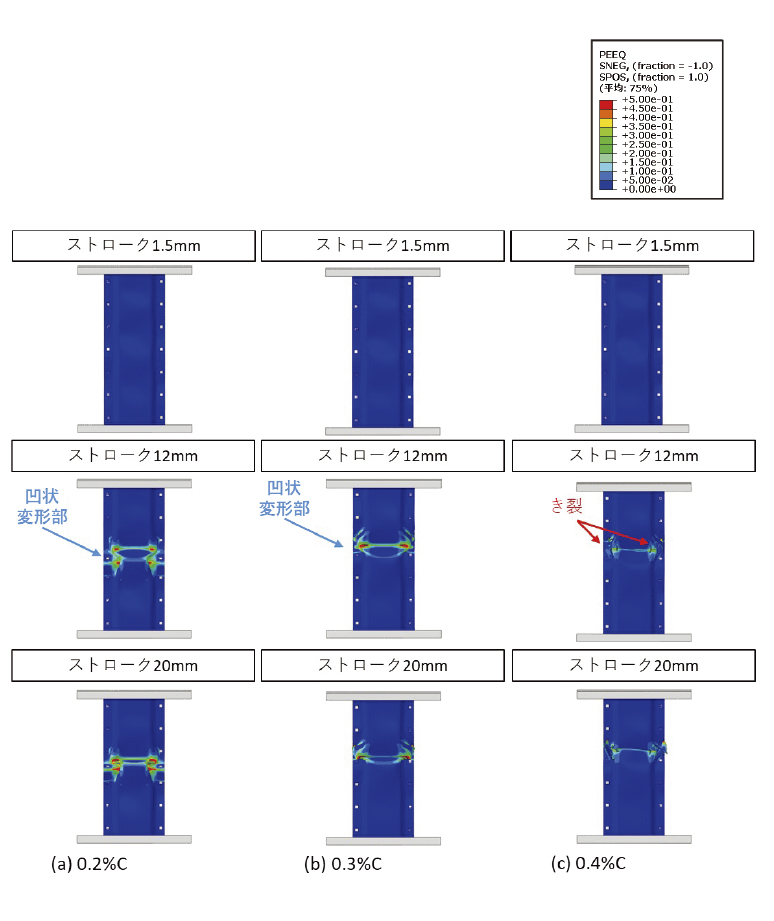
第9図 ストローク90mm 相当塑性ひずみ分布図
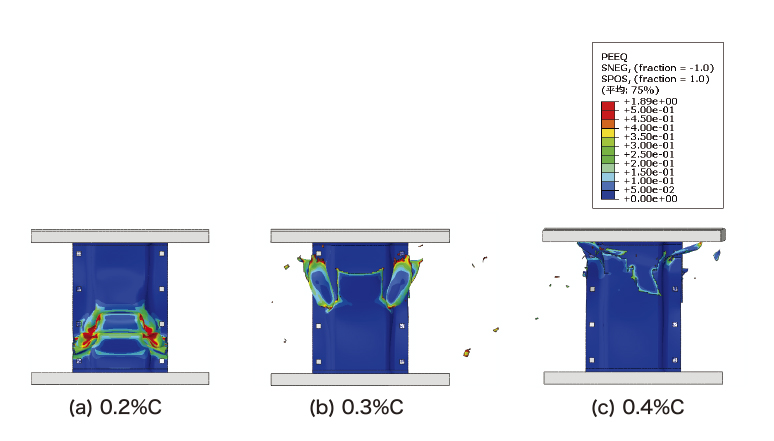
第10図 DICとFEMでの破断部周辺のひずみ履歴の比較
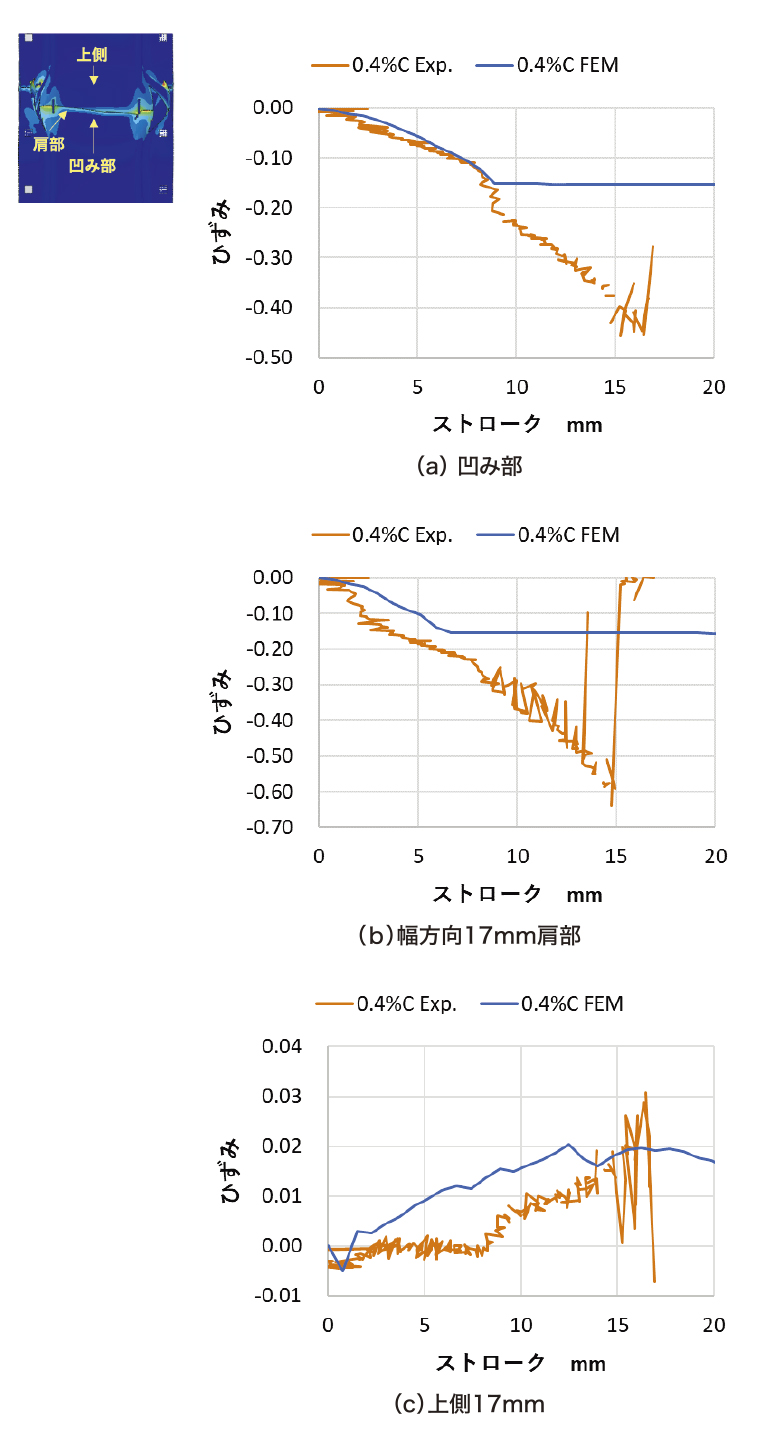
炭素量違いのホットスタンプ材に対して、その破断特性を取得し実部品を想定した試験体をもちいて軸圧壊試験を実施した。その結果、炭素量による破断ひずみの違いは平面ひずみや等二軸状態で大きくなっており、軸圧壊試験で得られる吸収エネルギー量の差にも表れていた。このことは、単軸引張試験だけでは板材の破断挙動の推定が難しい場合があり、応力状態を変えた破断特性試験や軸圧壊試験の実施が望ましいことを意味する。
また軸圧壊解析のFEMでは、材料モデルに破断特性を導入することで炭素量毎の割れや変形の特徴を再現できることを示した。今後も自動車ボディにもちいられる材料に対して、衝突破壊挙動の試験的評価やFEMモデル化について知見を深め、成果を適宜報告していきたい。
参考文献
- *1) 内藤純也ほか: R&D神戸製鋼技報,Vol.66(2017)No.2, p.69.
- *2) 井上功之ほか:自動車技術会秋季大会学術講演会予稿集, (2023)No.89-23.
- *3) Y. Bai et al.: Int. J. Fract.,Vol.161(2010)No.1,p. l-2.