コベルコ科研・技術ノート
こべるにくす
Vol.33
No.60
- TOP
- 技術ノート「こべるにくす」一覧
- アーカイブス
- アルミ鋳造品の鋳巣予測精度向上のための物性測定技術および湯流れ・凝固解析による鋳巣予測結果の紹介
Technical
Report
C
アルミ鋳造品の鋳巣予測精度向上のための
物性測定技術および湯流れ・凝固解析による
鋳巣予測結果の紹介
近年、モビリティ分野では複数部品を一体成形するギガキャスト製法が注目されている。いっぽうで、ギガキャスト製法は金型を含む設備に多大なコストがかかり、特にダイキャスト金型は一度製作すると大幅な形状変更への対応が困難である。そのため、大型アルミ鋳造品を砂型鋳造で試作および評価している報告例もあり、ダイキャストを含むアルミ鋳造品に対する注目度はますます高まっている。
アルミ鋳造品には凝固割れや鋳巣などの鋳造欠陥が発生するため、鋳造CAEをもちいて事前に部品形状や製造条件の検討がおこなわれている。鋳造CAEの解析ソフトウェアには、J-Mat-Proなどの熱力学計算ソフトにもとづく熱物性値がもちいられており1)、その値をもとにシミュレーションをおこなっている。さらに、解析精度向上のために解析モデルや基礎方程式の見直しなどによる改善が進められている2)。しかしながら、JIS規格の合金でも添加元素によっては成分範囲が広く、熱物性値にずれが生じることもあり、解析の予測精度にも影響をおよぼしていることが知られている。
そのため、当社では鋳造CAEの精度向上を目的とした、解析へ入力するさまざまな熱物性値を取得する評価手法の技術確立をおこなってきた。たとえば、固体の熱伝導率はレーザーフラッシュ法による測定が一般的におこなわれているが、溶湯を含む液体の熱伝導率を測定することは困難であった。鋳造CAEでは湯流れ性や凝固シミュレーションをおこなうため、液体の熱伝導率はCAEの精度向上に寄与すると考え、当社では溶融金属の熱伝導率も測定できるホットディスク法を開発した3)。
本稿では鋳造CAEによる鋳巣の予測精度に着目し、砂型アルミ鋳造品の試作と、鋳造CAEの解析ソフトウェアにあらかじめ入っている熱物性値と当社で鋳造用合金の熱物性値を測定した値とで比較した結果を紹介する。
C-1 砂型アルミ鋳造品の試作と鋳巣調査
試作用合金はエンジンブロックやバッテリーケースに使われているADC12とし、砂型アルミ鋳造品の試作をおこなった。ADC12の化学成分を第1表に、試作用の砂型の図面と外観を第1図~第3図に示す。試作型は左右2個取りとし、1個は流路や製品部の鋳造~凝固過程の温度測定をおこなった。温度測定位置を第4図に示す。また、鋳巣は最終凝固部に発生するため、板厚15mmの単純厚板製品に高さが異なるボス(高さ:6mm、9mm、15mm)をつけ、ボス直下を溶湯補給のない最終凝固部となる形状とした。
試作品の外観を第5図に、X線透過撮影画像を第6図、第7図に、浸透探傷試験結果を第8図に示す。鋳巣は9mmボス部の位置に集中しており、6mmボス部と15mmボス部の位置では確認されなかった。
第1表 ADC12の化学成分(wt%)

第1図 試作用砂型図面
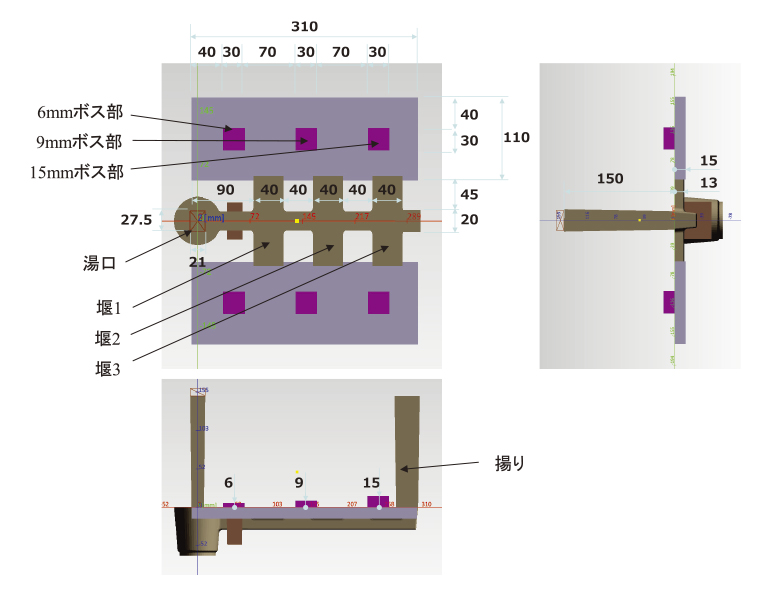
第2図 試作用砂型
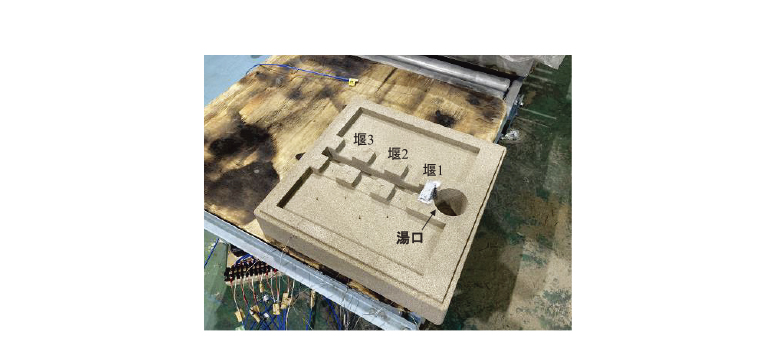
第3図 試作用砂型(上型)
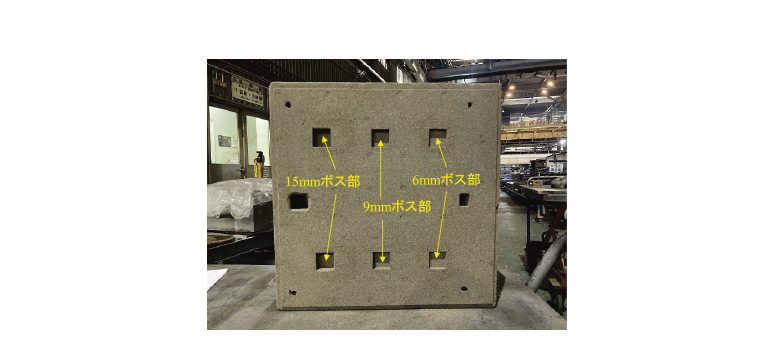
第4図 温度測定位置
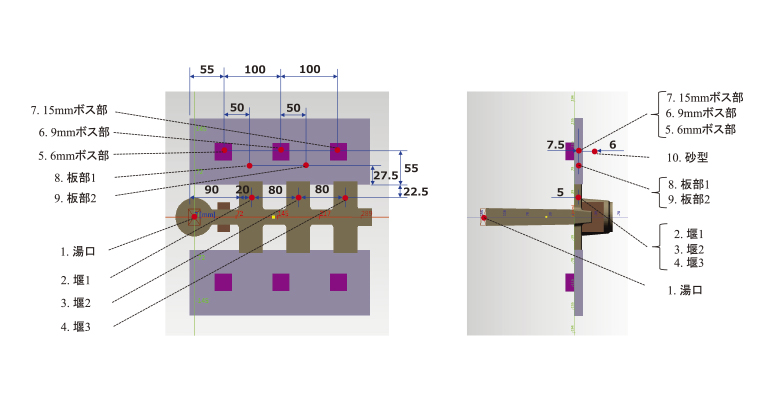
第5図 砂型アルミ鋳物試作品
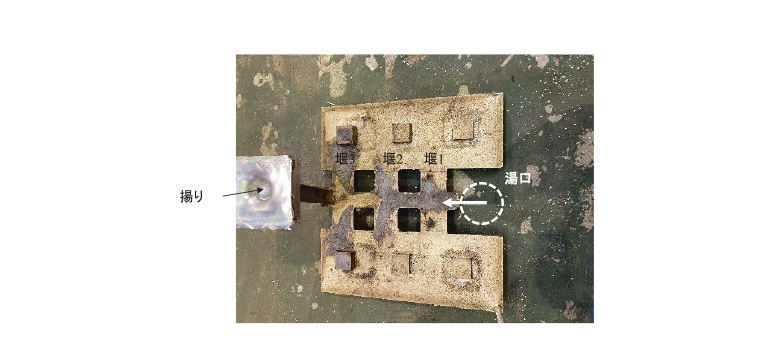
第6図 X線透過撮影画像
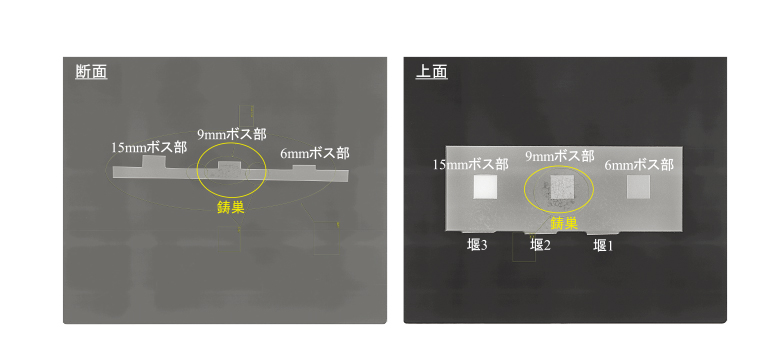
第7図 X線透過撮影拡大画像
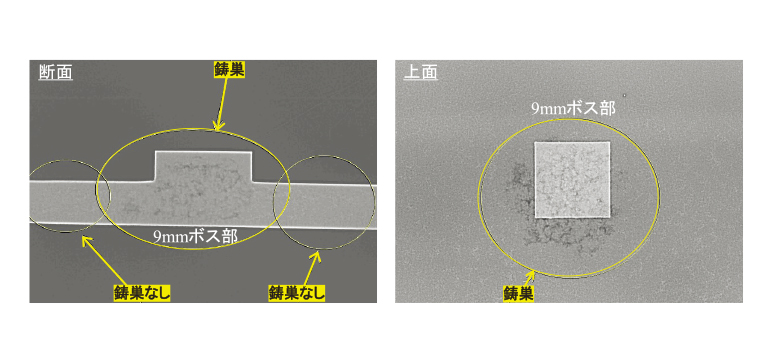
第8図 浸透探傷試験結果
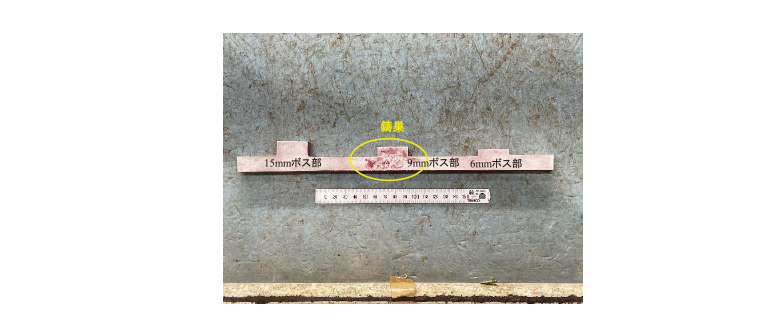
C-2 鋳造CAEによる鋳巣予測
鋳造CAEで第1章の砂型鋳造を模擬した解析をおこない、鋳巣の発生位置を予測した。解析にもちいたソフトウェアはMAGMASOFT(Ver.5.4.2.0)、熱物性値はMAGMASOFTのデフォルトデータと当社で取得したデータの2ケースで解析をおこない、鋳巣の予測精度を比較した。
2.1. 熱物性値の取得とデフォルトデータとの比較
当社で取得した熱物性値は、試作にもちいたADC12の室温~ 750℃における温度依存性を含む比熱、熱伝導率、密度を測定した。比熱はDSC法とし、測定結果から温度と固相率の関係も算出した。熱伝導率は室温~ 480℃の固相域をレーザーフラッシュ法、600~ 750℃の液相域をホットディスク法で測定した。また密度は室温と600~ 750℃の液相域を液中置換法で測定し、100~ 480℃の高温の固相域は試料の体積をTMA法で測定した熱膨張率より補正して算出した。
MAGMASOFTのデフォルトデータと当社で取得した熱物性値の比較を第9図に示す。当社で取得したデータのほうがいずれの熱物性値も低い傾向を示した。固相率は、液相線温度で約10℃、固相率0.3~ 0.8では約20℃の差がみられた。また比熱は約300~ 400℃、650~ 750℃において当社で取得したデータのほうが低い結果であった。いっぽうで、熱伝導率と密度には大きな差異は認められなかった。
第9図 各物性値の比較

2.2. 熱物性値の違いによる解析結果の比較
2.2.1 湯流れ解析結果
MAGMASOFTのデフォルトデータをCase1、当社で取得したデータをCase2として湯流れ解析をおこなった。注湯開始から0.5秒、1.0秒、2.0秒、3.0秒における湯流れの状況と溶湯温度を示した結果を第10図に示す。Case1では、0.5秒で溶湯が堰3に衝突するほか、主に堰1から溶湯が流入していた。いっぽうで、Case2はCase1に比べて粘性が高く、1.0秒でも溶湯は堰3に到達しておらず堰1から順に流入しており、Case1とは異なる傾向を示した。鋳造時に溶湯が流入する際の温度測定結果を第11図に、また各温度計測部位の最大温度および検知時間を第2表に示す。Case1は湯流れ解析結果と同様に、各堰(せき)、各ボス部の検知順序は実測と一致していた(堰3→堰2→堰1、15mmボス→9mmボス→6mmボス)。いっぽうで、Case2の検知順序は実測とは逆転した結果であった。
Case2は、Case1にくらべて650℃以上の比熱が低いため、注湯開始後に溶湯温度が早期に低下して粘性が高くなった結果、溶湯の流入速度が遅くなり実測とは異なったと考えられる。
第10図 湯流れ解析結果
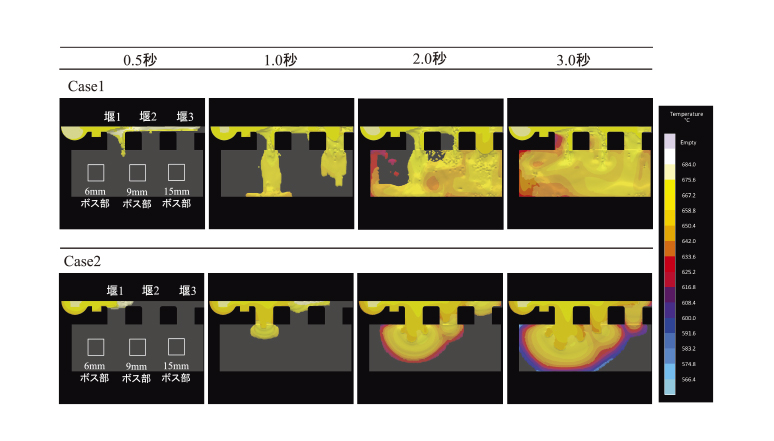
第11図 鋳造時の温度測定結果および解析による加熱曲線
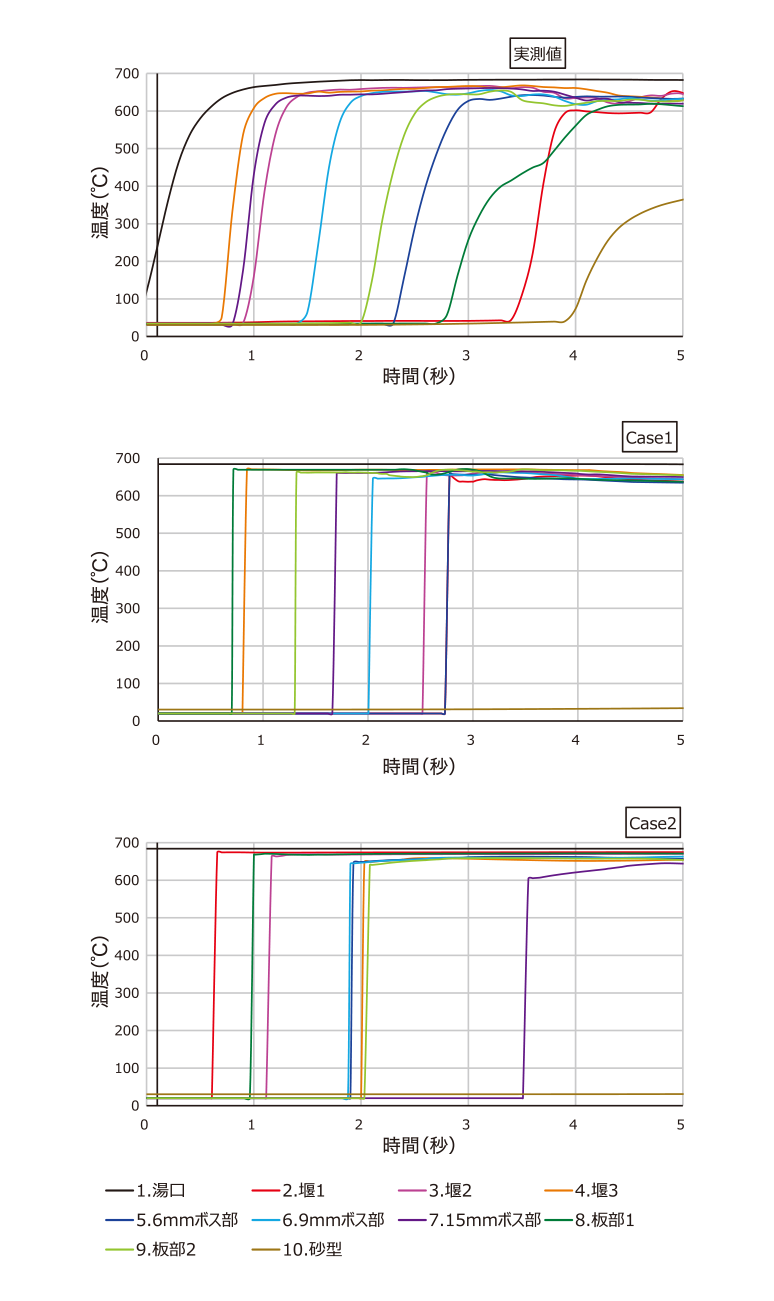
第12図 流動限界固相率到達時間解析結果
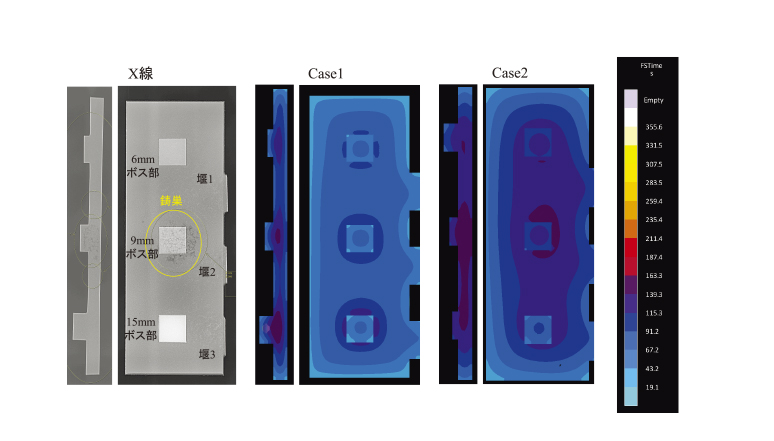
第2表 各部位における最大温度および検知時間

2.2.2 凝固解析結果
凝固解析による流動限界固相率到達時間の解析結果を第12図に示す。Case1では湯口から遠い15mmボス部付近で、またCase2では9mmボス部付近で到達時間がもっとも遅くなる傾向を示し、Case2のほうがX線画像と近い結果であった。つぎに、鋳造時の温度測定結果および解析による冷却曲線を第13図に示す。Case1にくらべてCase2のほうが、冷却曲線が実測に近い傾向を示した。第9図に示した温度と固相率の関係がCase1とCase2で異なっており、凝固発熱が起こる温度、また流動限界固相率に到達する時間に違いがあるため、冷却曲線や解析精度にも影響をおよぼした結果、Case2のほうが凝固解析結果の精度が高くなったと考えられる。
また、健全度を比較した結果を第14図に示す。第12図で示した流動限界固相率の到達時間が長い部位で健全度が低くなる傾向を示した。Case1では各ボス部とも健全度が低い結果であるのに対して、Case2では9mmボス部付近で集中して健全度が低い結果となり、試作品に近い結果が得られた。
このように鋳造CAE用のデータを変えた解析結果から、同じADC12でもデータの違いで解析結果が変わること、また当社で取得したデータをもちいることにより、鋳巣の予測精度が向上することがわかった。
第13図 鋳造時の温度測定結果および解析による冷却曲線
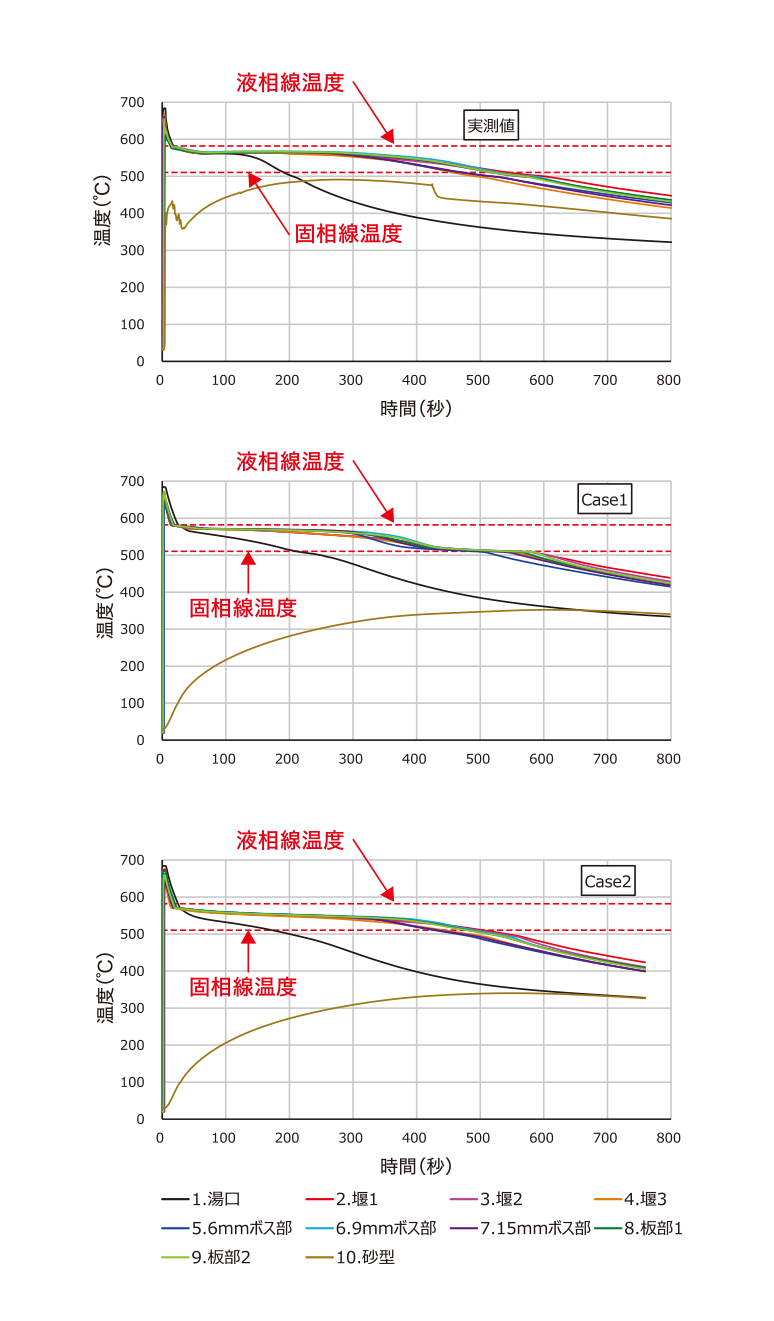
第14図 健全度解析結果
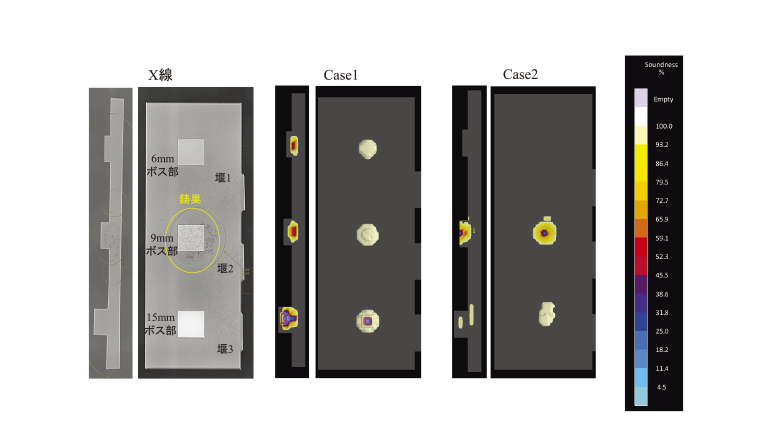
今回の鋳造CAEではCase1、Case2ともに砂型の熱物性値や砂型とアルミ溶湯の熱伝達係数などはMAGMASOFTのデフォルトデータをもちいている。そのため、今回取得した熱物性値以外のデータも実験により求めた結果を入力すると、今回実測と合わなかった湯流れ解析も含めてさらに予測精度を向上できる可能性はある。また、今回取得した熱物性値は、砂型だけではなくダイキャスト製品における鋳造CAEの予測精度向上にも寄与すると考えられることから、現在その試作と解析も進めている。
砂型やダイキャストなどアルミ鋳造品の車体への適用にあたり、衝突解析などの強度解析をおこなう上で、強度へ影響をおよぼす鋳巣発生位置の正確な予測も重要である。そのため、鋳造CAEによる予測精度の向上に対するニーズもますます高まることが予想される。今後もさらにお客さまの課題や要求に対して継続的な提案ができるよう、新たな技術開発にチャレンジしていく。
参考文献
- *1) 木島秀弥.鋳造工学,Vol.86,No.12,(2014)p.951-956
- *2) 三中西信治.鋳造工学,Vol.95,No.1,(2023)p.34-40
- *3) 足立渉ほか.こべるにくす,No.55,(2022)p.19-20